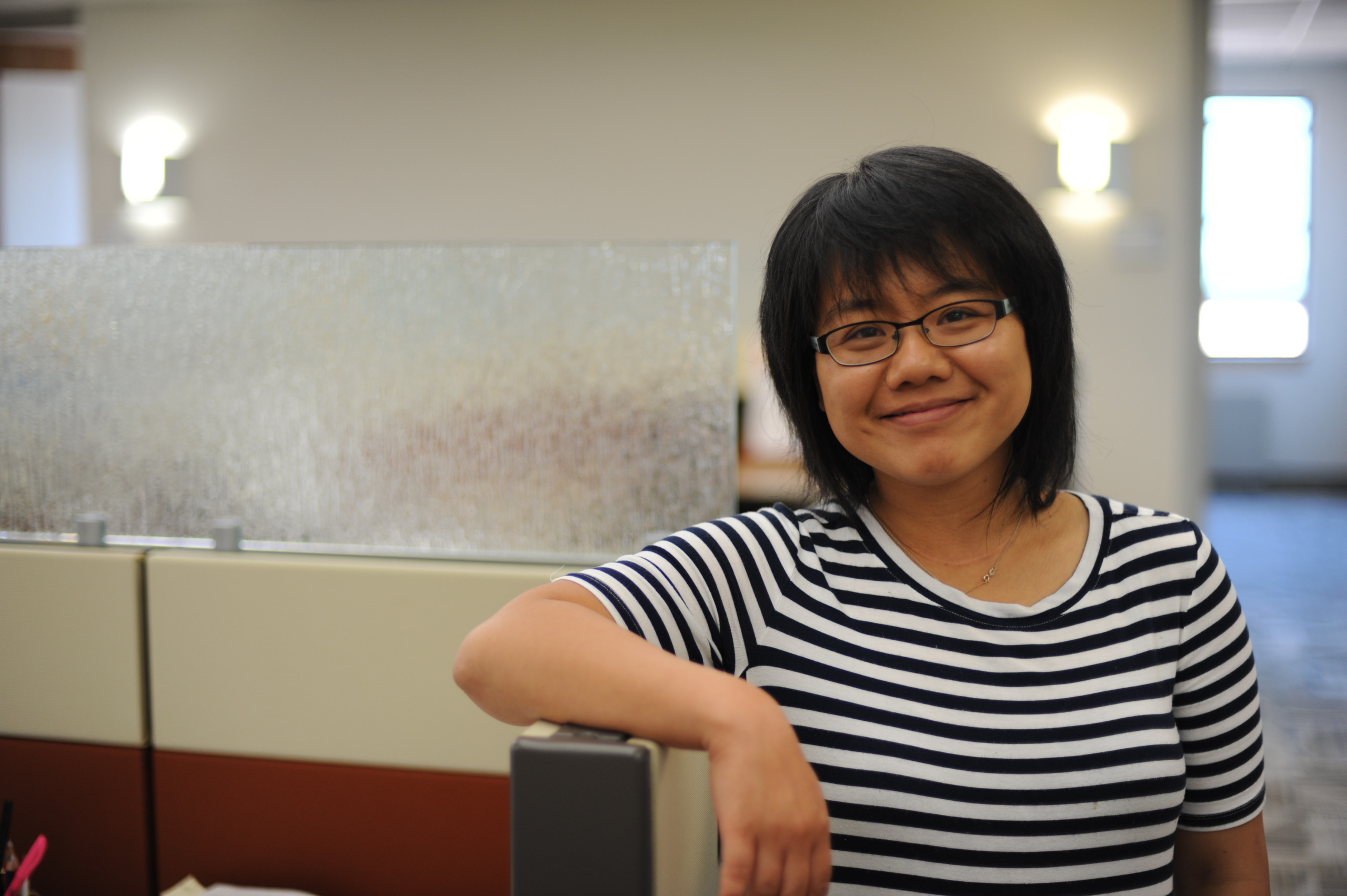
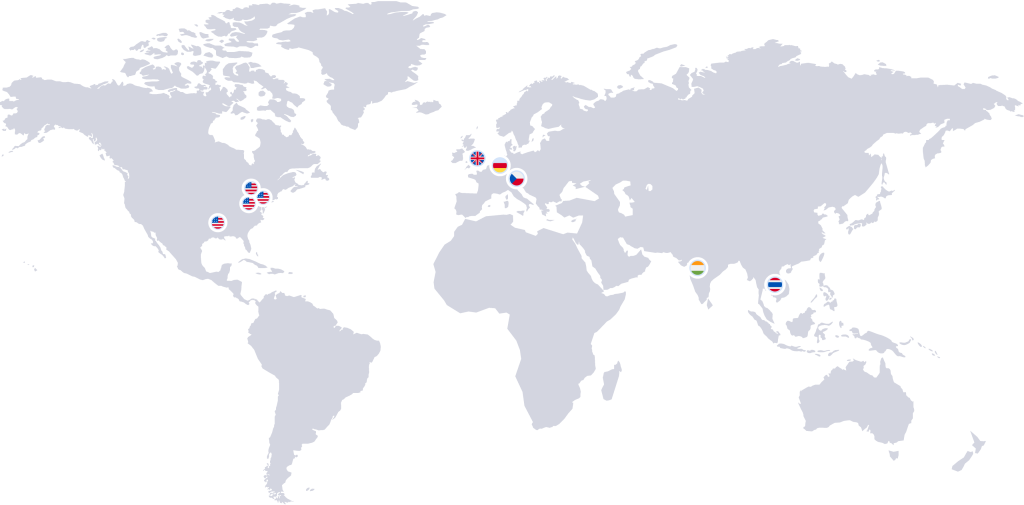
Our Global Reach
Custom Service Close to Home
We’ve worked to establish ourselves as a prominent global partner, operating in the United States, United Kingdom, Germany, Czech Republic, India, and Thailand. Our accessibility to a wealth of geographic locations allows us to provide consistent and reliable service to our customers, whenever and wherever they need it.
Locations
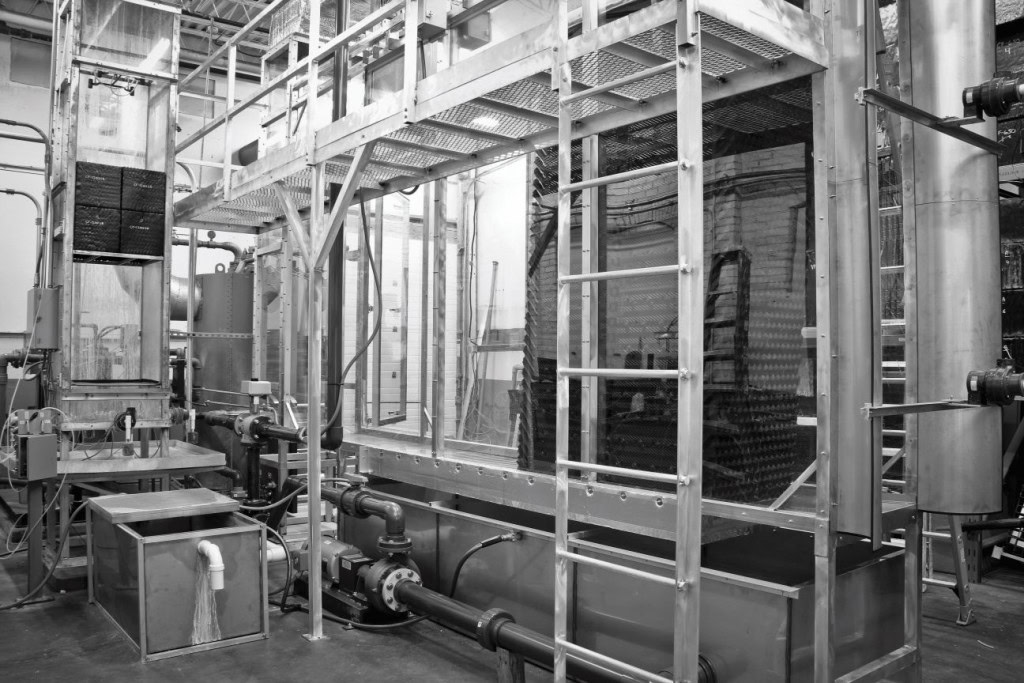
Research & Development Lab
Brentwood understands the power of testing and research & development (R&D). We invest heavily in these core areas of our business so we can develop new products and improve existing ones.
Our headquarters houses our state-of-the-art R&D lab. It is fully staffed by engineers and scientists, capable of evaluating everything from material properties to strength and performance.
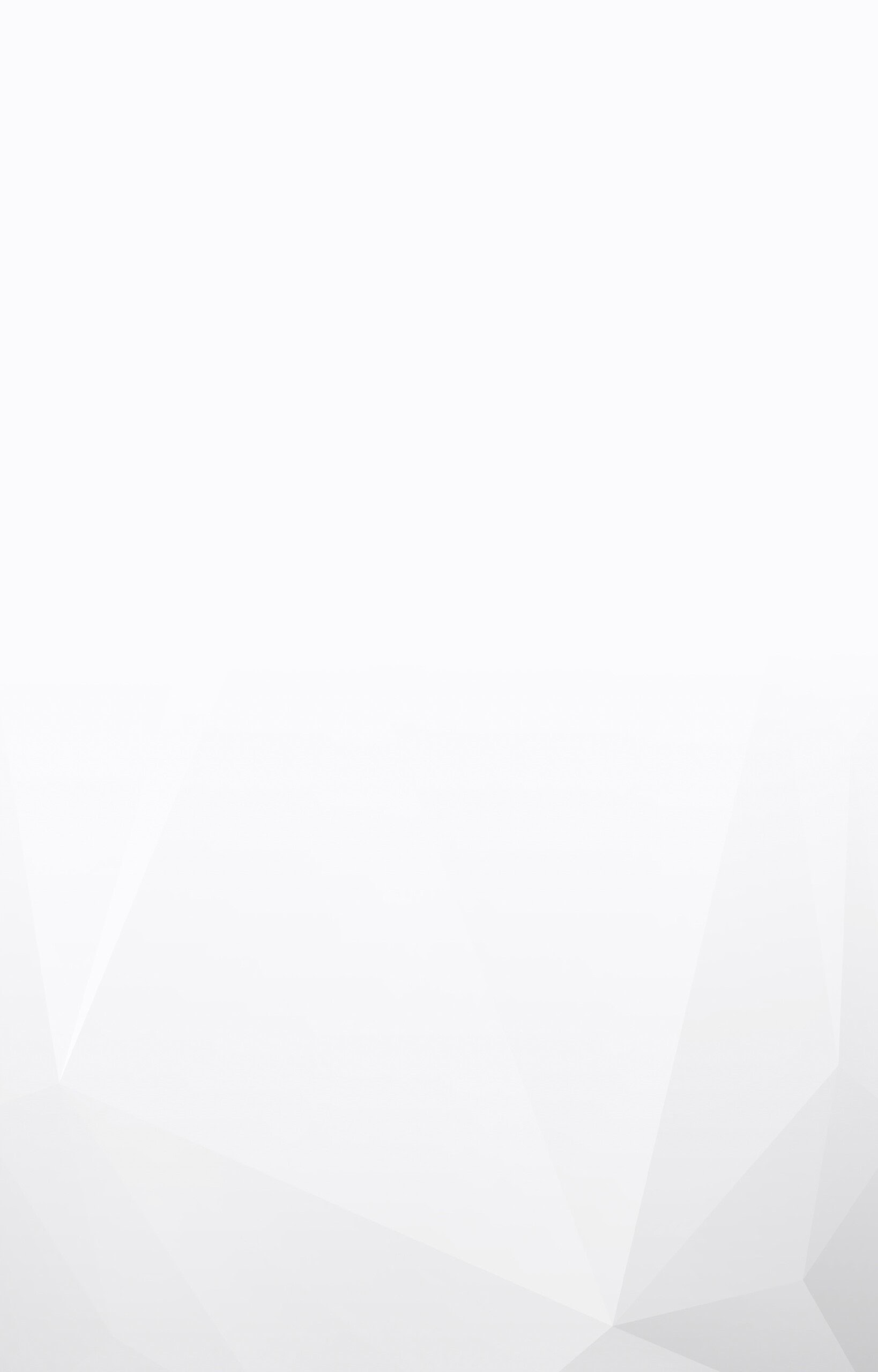