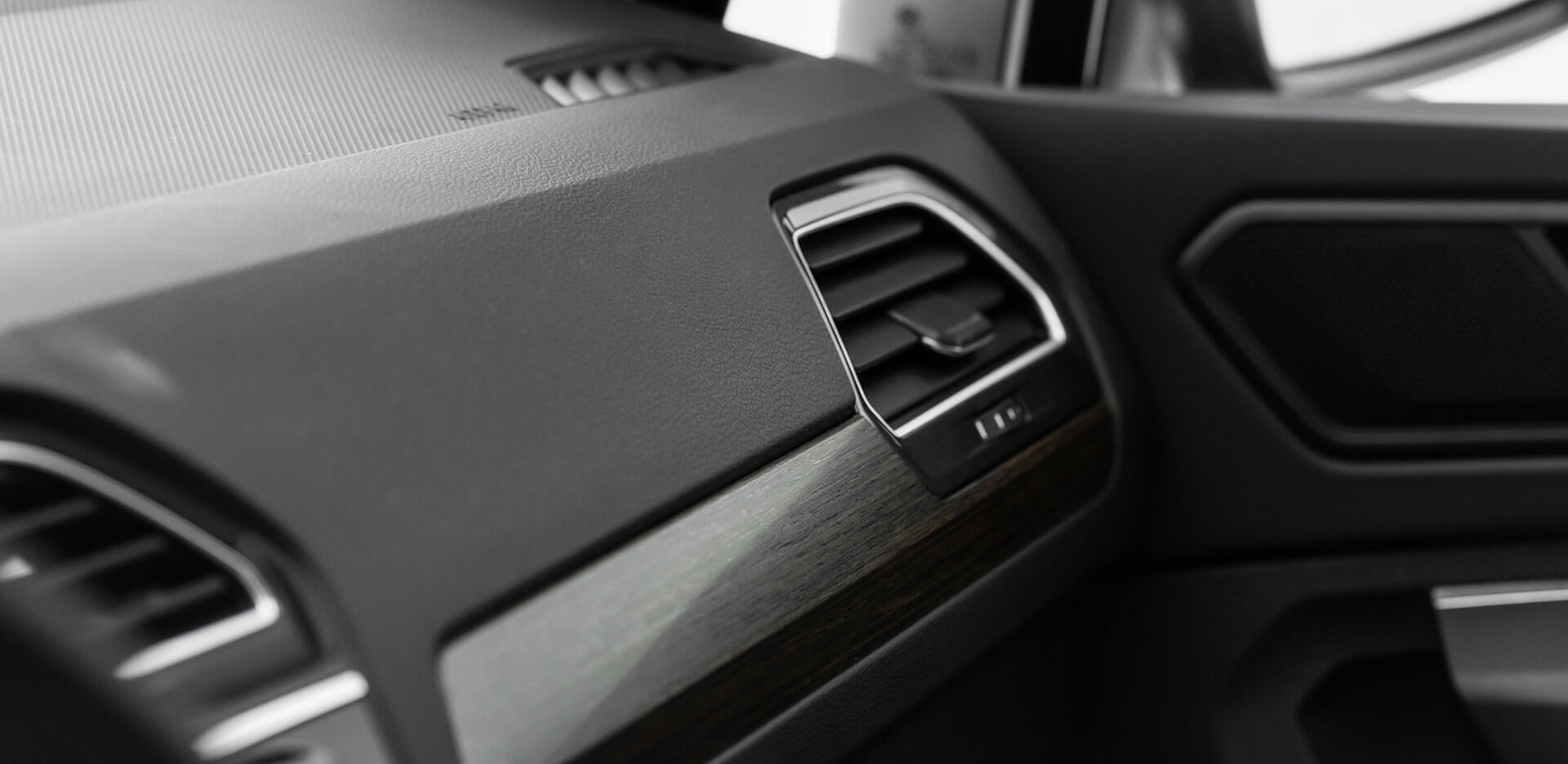
Solutions
Automotive
Thermoformed parts offer a durable, lightweight solution for use in the automotive industry, both inside and outside the vehicle. Brentwood can form both light- and heavy-gauge parts, from dashboards and air ducts to bumpers and exterior panels.
Heavy Truck
Brentwood can produce anything from door panels and dashboard coverts to fenders, splash guards, and bumpers for the heavy truck industry. We also perform in-house secondary operations, such as assembly, that enable us to deliver a semi-finished product to the customer.
Railcars
Brentwood is an experienced manufacturer of functional and aesthetic interior trim and seating components for the railcar industry. We form low-flame, -smoke, and -toxicity materials and have completed technically demanding projects using anti-graffiti and decorated films.
Aircraft
Much like the railcar industry, Brentwood forms plastic products for airline seating components, such as tray tables, seatbacks, and arm rests. These are designed to be lightweight, cosmetically appealing, and flame retardant.
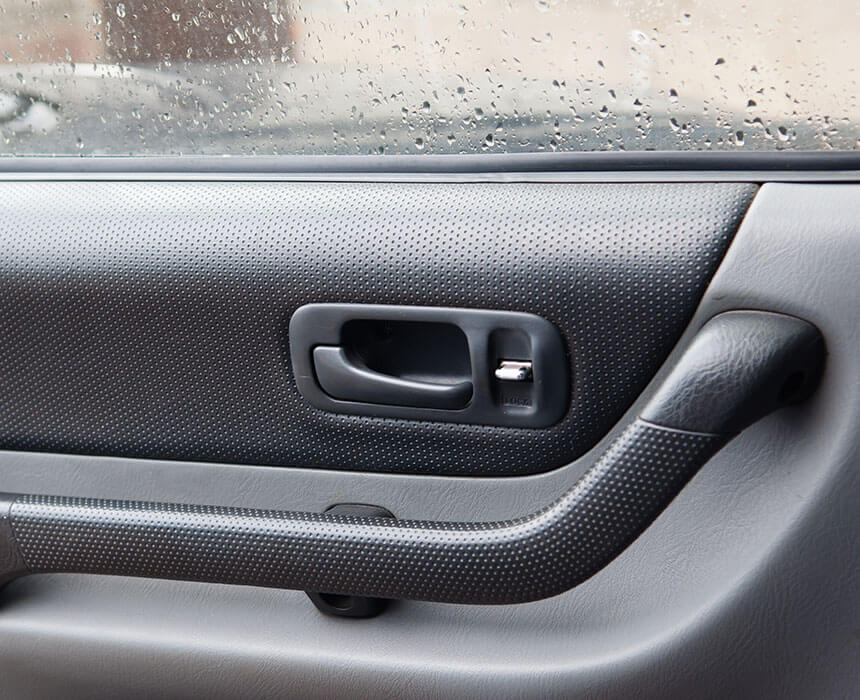
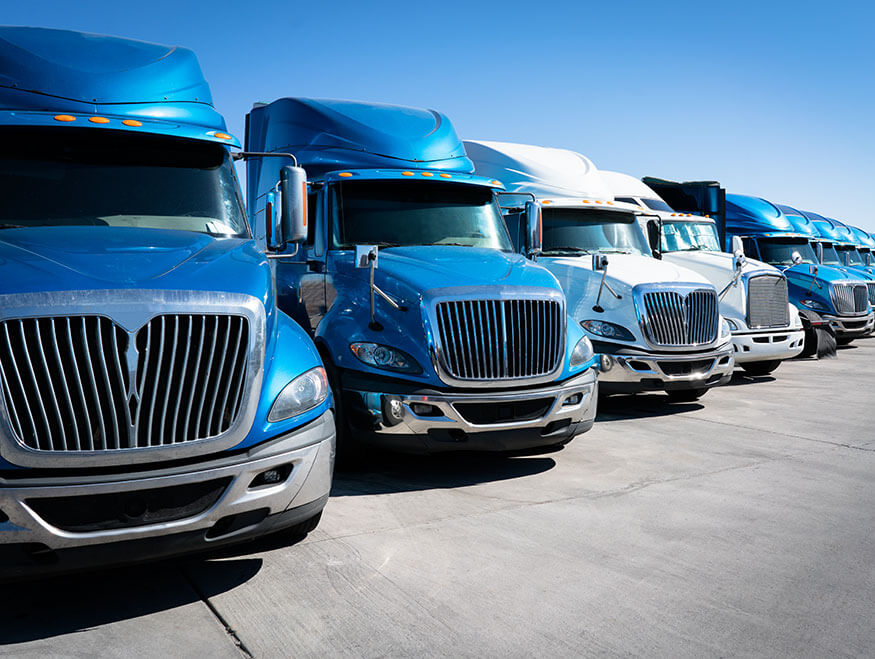
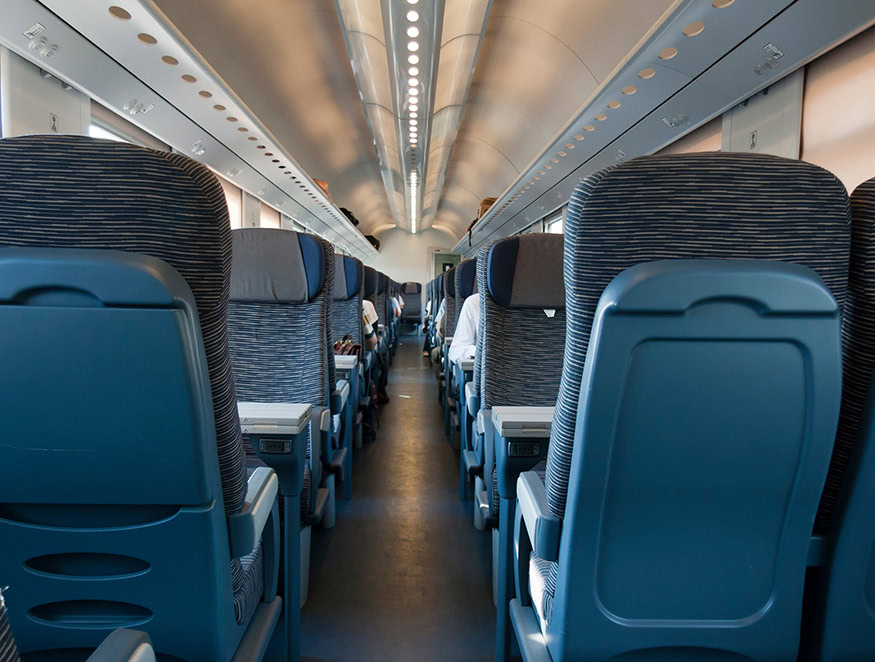
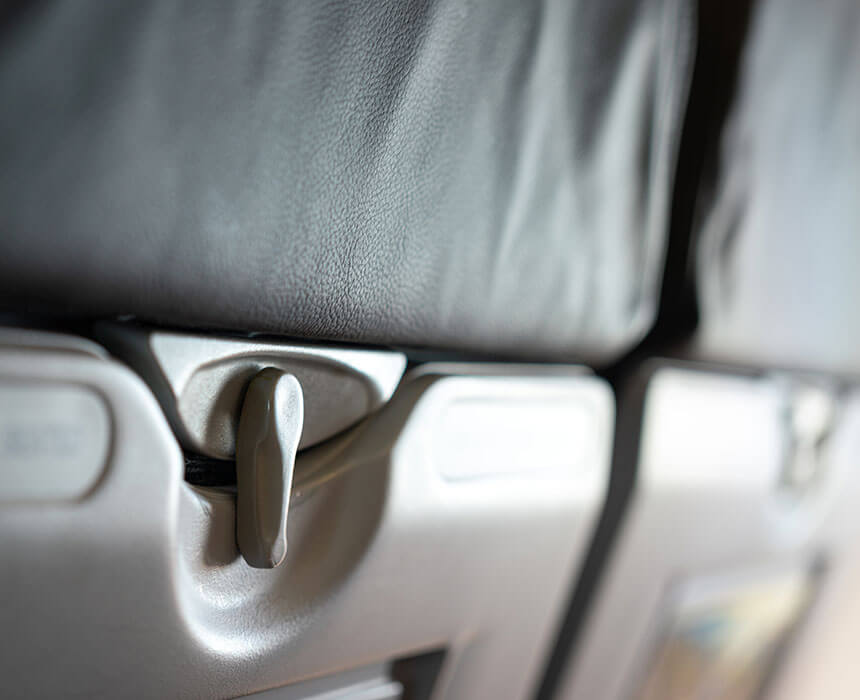
Products
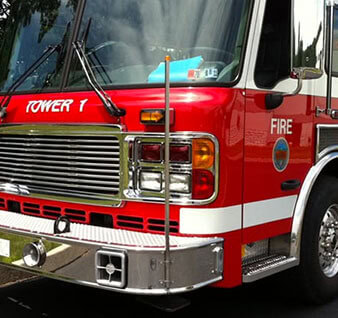
Bumpers & Fenders
Designed for aesthetics, impact resistance, and integration with numerous other parts, Brentwood has formed bumpers for automotive and heavy truck applications.
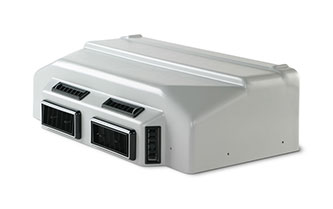
Dashboards
Brentwood designs dashboard panels in a range of colors, materials, textures, and with built-in air vents and components.
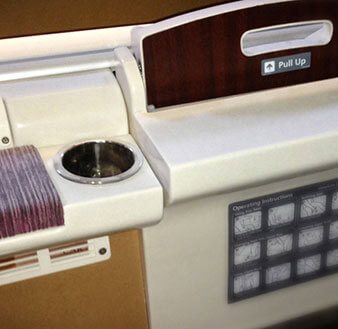
Interior Panels
Interior panels and consoles are designed with long life in mind. In some applications, they need to be not only lightweight and aesthetic, but also graffiti-resistant.
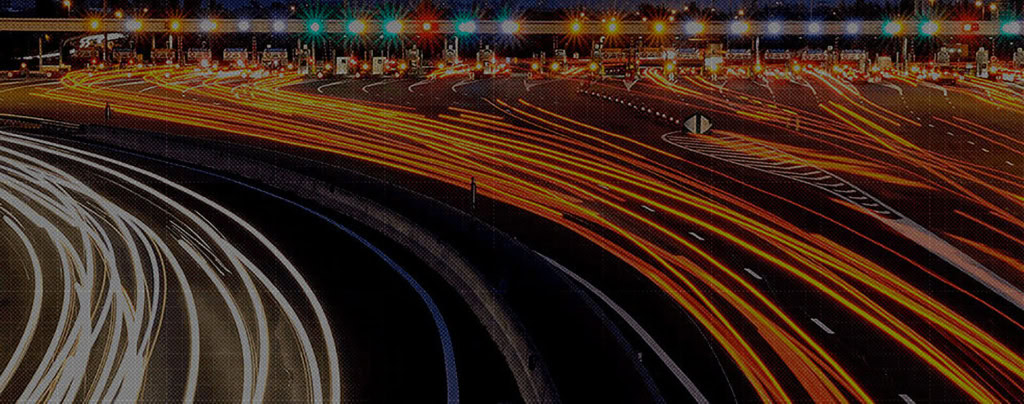
Custom Solutions for Transportation
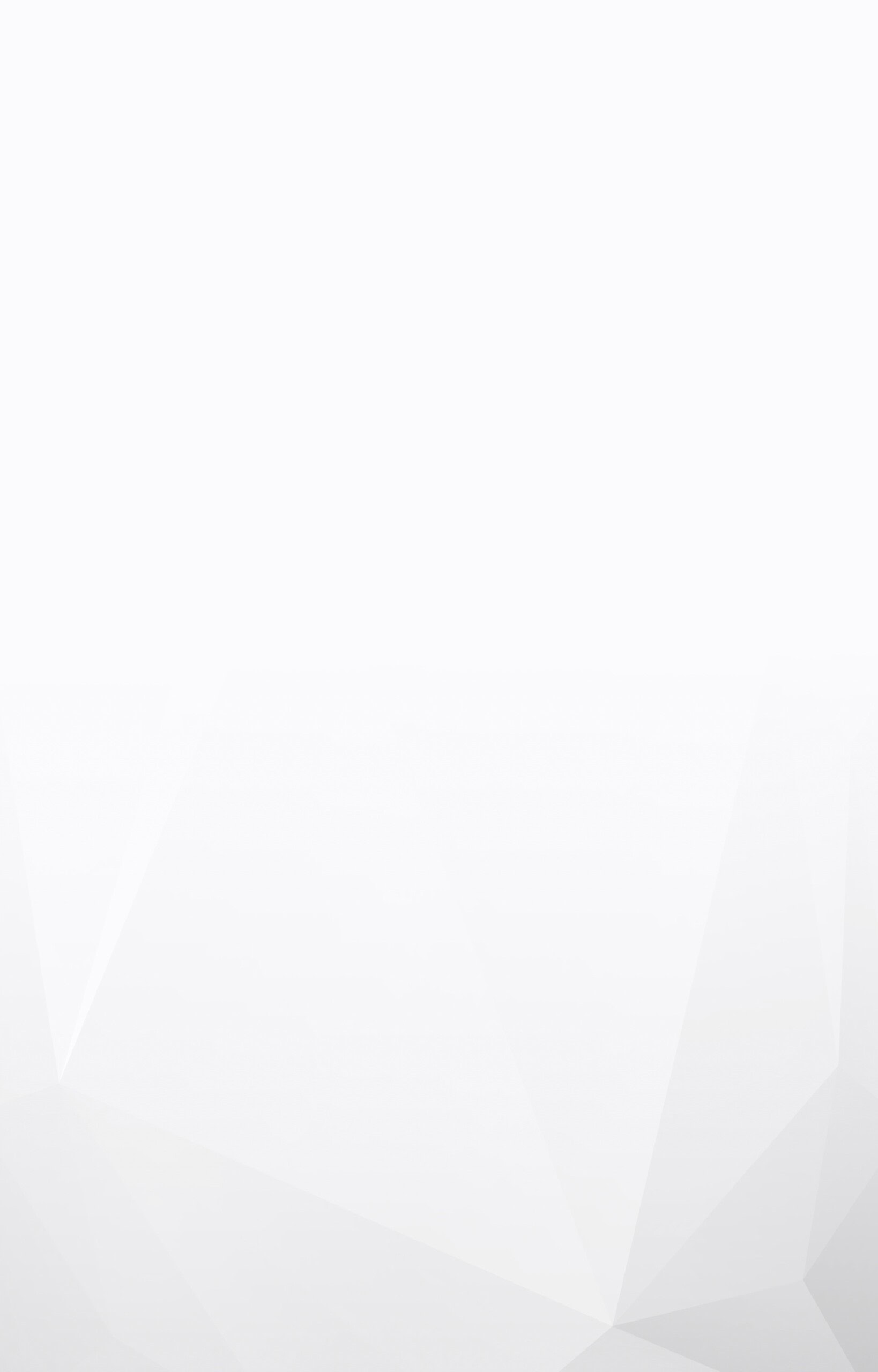