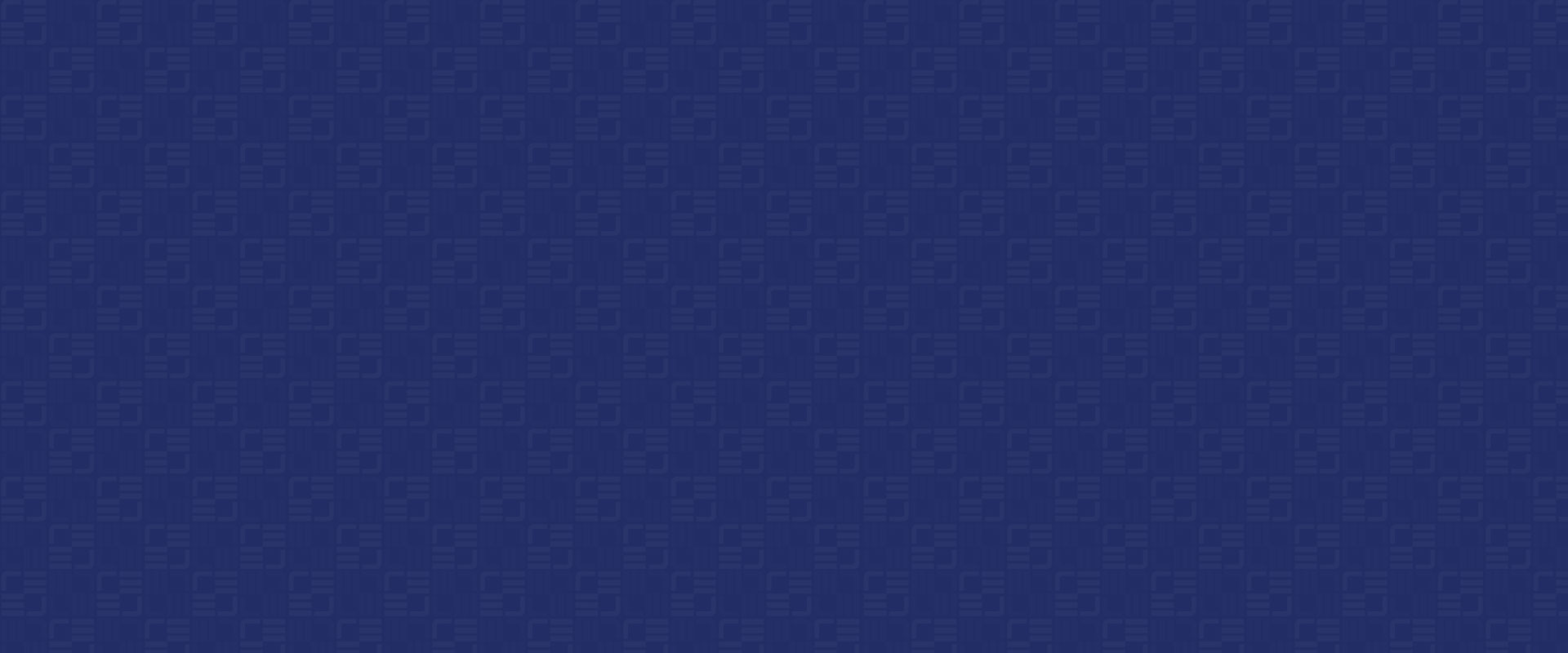
Categories: Water & Wastewater.
Quality is an attribute that has been used to differentiate superior products for centuries. However, in the modern production facility, quality has transcended from a nebulous comparison to both a profession and philosophy.
Over the past 70 years, manufacturers (with the help of a few pioneers) have been asking more insightful questions about quality. This journey created a holistic system that utilizes statistics, science, and management principles presently known as quality management systems (QMS).
Origin of the Quality Movement
The modern QMS owes itself to a few key innovators including Joseph M Juan, Phillip Crosby, Walter Shewhart, and W. Edwards Demming, who were the first to recognize the importance of an analytical approach to quality. They developed statistical controls and management approaches that aimed to improve production, product reliability, and set achievable and measurable quality goals.
After WWII, Japanese companies began utilizing these concepts to great effect. The commitment of these companies to quality as a concept helped differentiate their products in the marketplace.
Following the success of their Japanese counterparts, American companies and others (notably the Ford Motor company) began implementing the same principles. This focus on quality led the United States Congress to establish the Malcolm Baldridge National Quality Award in 1987, which recognizes and distinguishes U.S. companies who instate a successful QMS. This honor helped spur development in the United States.
Quality Today
The modern QMS borrows heavily from its original founding concepts. Quality management systems must still include the entirety of an organization. They maintain the importance of statistical process control, management commitment, and clear and measurable expectations with a focus on continuous improvement. Additionally, active participation with no fear of sharing or documenting problems remains a key element. However, the modern QMS has evolved to fit the needs of individual businesses.
What Makes a Good QMS?
There is not one checklist that defines a good QMS. What makes a QMS successful is adherence to principles and recognizing the importance of consistent quality. Many good QMS models exist that give organizations great guidelines to follow – but one size does not fit all. Several independent organizations have created certifications that allow outsiders to assess the credibility of a manufacturer’s QMS. One of the most renowned institutions is the International Organization for Standardization (ISO).
ISO & ISO 9001
The International Organization for Standardization, known as ISO from the Greek word “isos” (equal), was established to address a globalizing world. It has grown into an independent organization that establishes standards and best practices to create some uniformity among various manufacturing sectors.
Currently, ISO committees possess standards for many different industries, and maintain a respected position throughout the world. One standard is ISO 9001, which specifically addresses a company’s QMS. ISO 9001 is a generic set of standards that establish best practice protocols for a QMS. Any company is welcome to follow the standards, but certification requires independent auditing every two years. It should be noted that the ISO organization itself does not perform audits.
Obtaining a certification is no easy feat and requires significant time and financial investment on the part of the manufacturer. A certified QMS requires every aspect of an organization to think about quality and commit to the protocols that are developed. Third party auditors make sure that ISO 9001-certified manufacturers follow the documentation and control techniques established in the company’s QMS. Non-compliance can result in revocation of a company’s certification. An ISO 9001-certified QMS is the best available certification to ensure that a company is upholding its quality control commitment.
Assessing a QMS
Standards, like ISO 9001 with third party certification, give end users and specifiers a quick snapshot into the accountability and mastery a company applies to their QMS. While not possessing a third party certification is not necessarily grounds for dismissal of a particular product, many sectors have adopted third party certification of ISO 9001 compliance as a requirement. In lieu of a certification, specifiers and end users should review the company’s quality control plan, the documentation created, and the corrective actions within the documentation. Additionally, overall commitment can be assessed by the specific quality knowledge demonstrated by a company’s management.
By providing our customers with the knowledge we have has gained on our own quality journey, we hope to empower those we serve. Brentwood’s certification list can be viewed on our website.
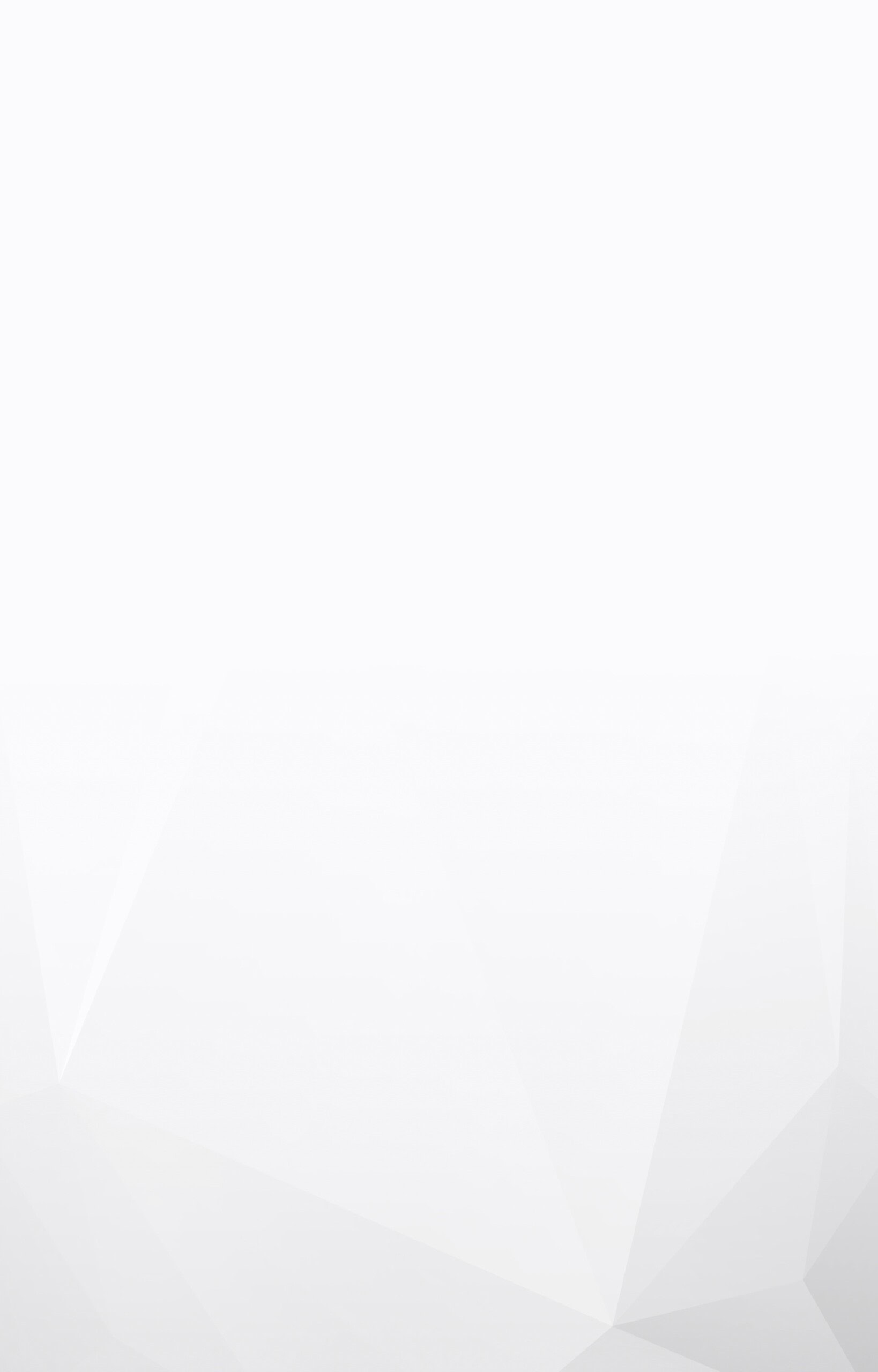