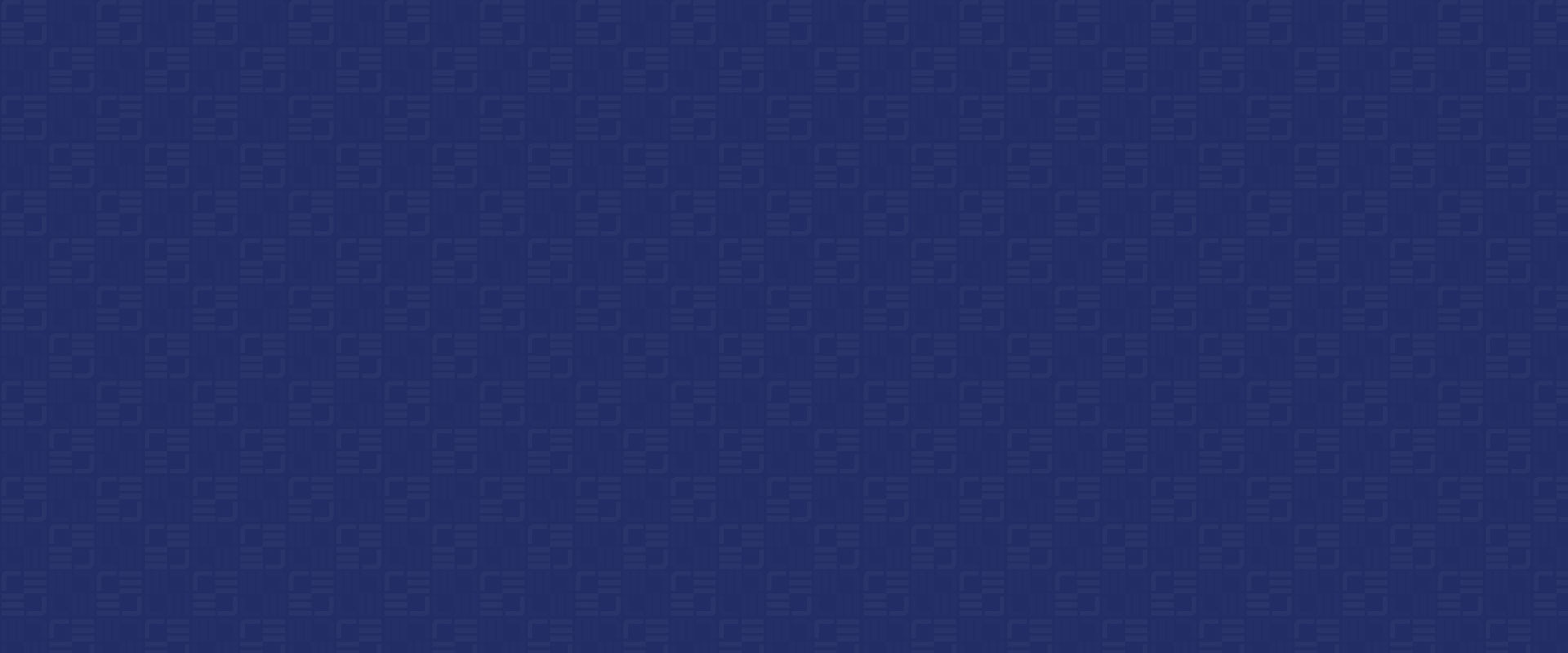
Categories: Water & Wastewater.
When choosing plastic media for trickling filter applications, are you thinking 20-30 years ahead? Too often, upfront cost is the
How do you know that the media you’re getting is structurally sound and built to last? We’ve compiled a checklist of the top five indicators of module strength to look for when specifying media for your trickling filter application:
- Material Properties
Let’s start with the most granular consideration: material properties. Plastic characteristics should be tightly spelled out in a media specification. When it comes to assessing media quality, tensile strength and flexural modulus are key indicators of a material’s strength. Tensile strength is the stress level a polymer can withstand without permanent deformation. Flexural modulus measures a material’s stiffness, or resistance to bend, when force is applied perpendicular to the long edge of a sample.
Bending deformation is the major mechanism that leads to trickling filter media failure, so the flexural modulus is the most important parameter for evaluating the media’s ultimate strength.
- Gauges
Gauge refers to the thickness of an individual sheet. Generally speaking, a thicker gauge translates to a heavier, stronger module. But strength fluctuations may exist even if a material claims to meet a specific flexural modulus. While module weight is important to look at, it should not serve as the sole indicator of strength.
If you are specifying a gauge requirement, there are a few factors to keep in mind. Take a look at how that particular gauge has been used and the design load it has been used in. Gauges typically come at a pre-forming thickness. However, plastic is essentially stretched out when fed through a thermoformer, creating a separate post-forming thickness measurement. When examining gauges, remember to take both pre- and post-forming thicknesses into account and consider the ratio between the two.
- Tolerances
A misaligned pack will bear weight unevenly and can lead to inefficient performance or failure. This can be detrimental to structural integrity. Be sure to specify that a percentage of modules be pulled aside on-site and their faces, widths, and lengths be tested for tolerance.
- Compression Testing
Compression testing is used to determine media module strength, as long as the media modules are sufficiently designed to account for the load and creep over time. Compression testing provides the best indicator of media strength and life. Not only are plastics viscoelastic, but their behaviors change based on their formulations. Not all plastics are the same; different suppliers will have different formulations. The purpose of compression testing is to ensure that a system’s design load is met. It is imperative to confirm that a media pack can withstand the conditions that it was designed for.
At Brentwood, we perform compression tests by setting four media packs in right angles next to each other to simulate the actual layout of media in a trickling filter. Cross linkage is important to ensure an accurate simulation and provide the best glimpse into a real-life application. We then apply a setting load for an hour. After the setting load, the load is increased until 3% deflection, or ultimate failure. This test provides a load versus deflection curve that can be used to determine the media module’s strength. There isn’t one perfect method to model a 20–25-year design life, but compression testing is the closest way to replicate it and is the best indicator of pack strength.
Quality Assurance
While compression and tolerance testing are good measures to state, it isn’t feasible to test every individual piece of media going into a trickling filter. Therefore, a manufacturer with a third-party certified quality management system (QMS) in place, like ISO9001, is a great way to ensure consistent quality. A QMS benefits specifiers, end users, and manufacturers alike. We provide more detail into the importance of a QMS in our blog: Understanding Quality Management Systems (QMS).
While not all encompassing, our top five considerations outlined above will help you to holistically assess the quality of a supplier and their media. When specifying media, the best method is to understand the factors that contribute to media module strength and longevity and provide a means for these to be verified. Proper media and design can ultimately cut down on the number of tanks required and increase cost savings. Brentwood has a team of in-house engineers ready to support your application and assist with process design and specifications. Reach out to us here with any questions!
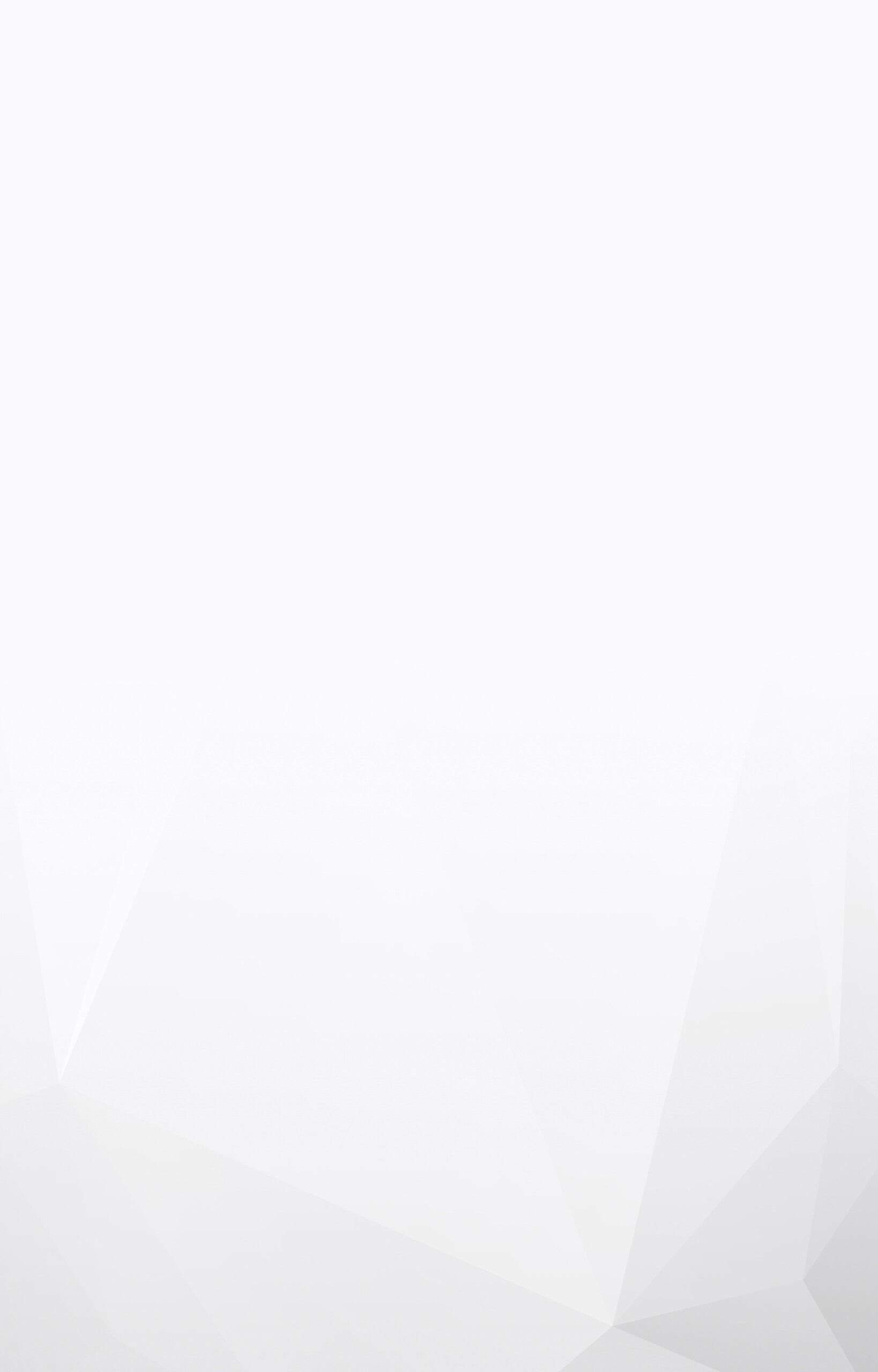