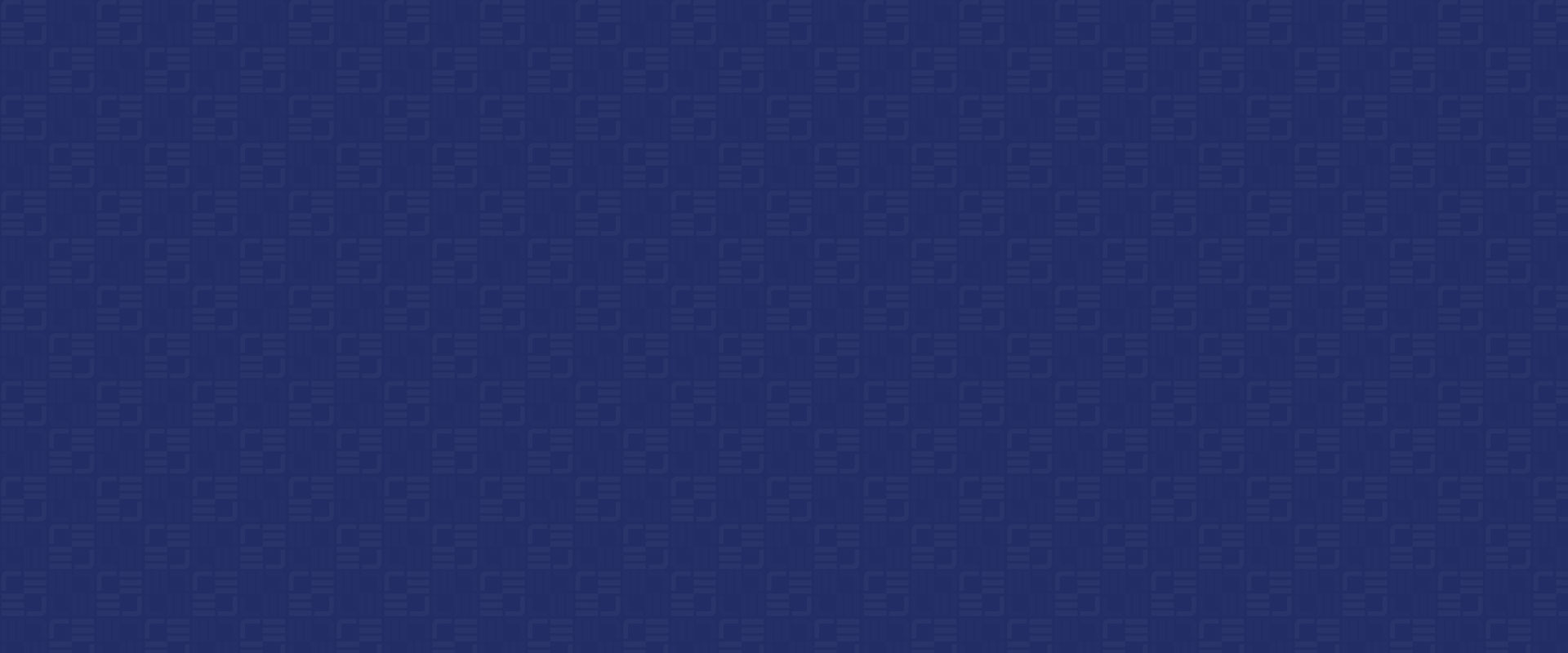
Categories: Water & Wastewater.
T
Module Design
Brentwood produces tube settlers using the thermoforming process, which heats a sheet of plastic to make it pliable so it can be formed into a specific shape. While the formed shape may differ slightly between manufacturers, the basic premise is to create a sheet with corrugations. Some manufacturers take that corrugated sheet and join it to a flat sheet to build a module by alternating corrugated and flat sheets.
Brentwood has taken this design a few steps further, resulting in stronger tube settler modules. A simple comparison would be building a bridge using toothpicks and glue. A strong bridge can be made by using many toothpicks and a lot of glue. However, with some engineering and ingenuity, an equally strong bridge can be built using less material. Therefore, instead of relying on a flat sheet of plastic between the corrugated sheets, Brentwood engineered and designed a “wave” sheet. This sheet features stiffening ribs at the top and bottom and dedicated glue joints for precise alignment between corrugated and wave sheets. The wave sheet also includes a curvature between the glue guides to provide a nesting effect for modules that are installed side by side. When installed correctly, this helps to transfer load to adjacent modules, increasing the overall structural integrity of the system. Brentwood’s corrugated sheets also contain stiffening ribs, a vertical return at the top and bottom, and a trapezoidal shape for improved weight-bearing capacity.
Manufacturing Process
While extruded tube settlers and thermoformed tube settlers generally perform in the same manner, they are designed and manufactured quite differently. The extrusion process takes a raw material, in this case plastic, and pushes it through a die to make a specific shape. (Think of making spaghetti with Play-Doh when you were a kid). The shape for most extruded tube settlers is generally a “V” with a tongue and groove on either side. After the shapes are extruded, they are assembled side by side as well as front to back, using the tongue and groove to connect them together, resulting in a chevron pattern. This type of design provides tubular channels much like thermoformed tube settler modules.
However, one significant difference between extruded and thermoformed tubes is that extruded tubes have no wave (or flat) sheet at all. This weakness in the design results in the need for a more robust and complex support system as they are not capable of meeting the same unsupported span as thermoformed tubes. In a majority of cases, this means the support system for extruded tube settlers will have much higher material and installation costs.
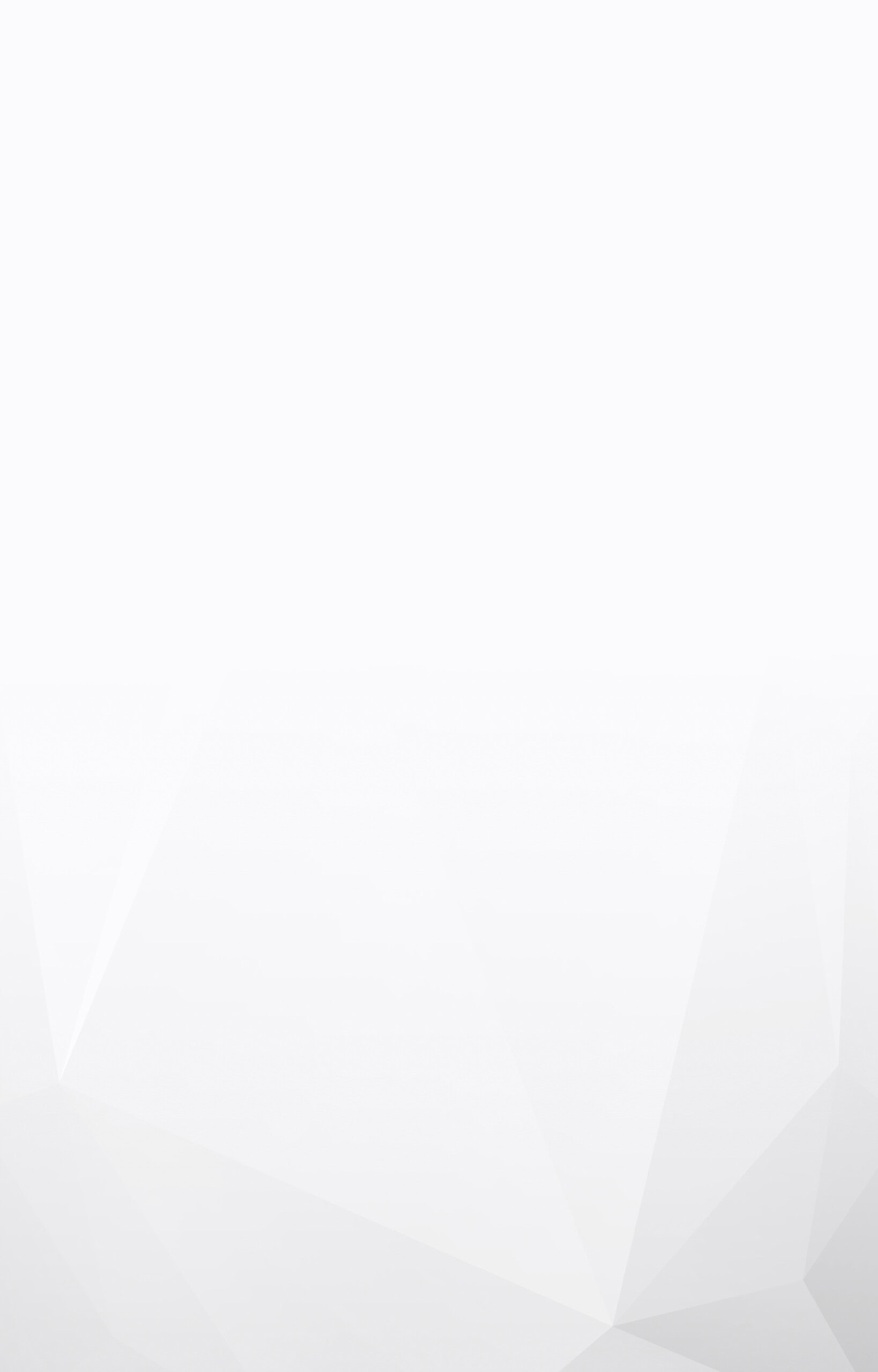