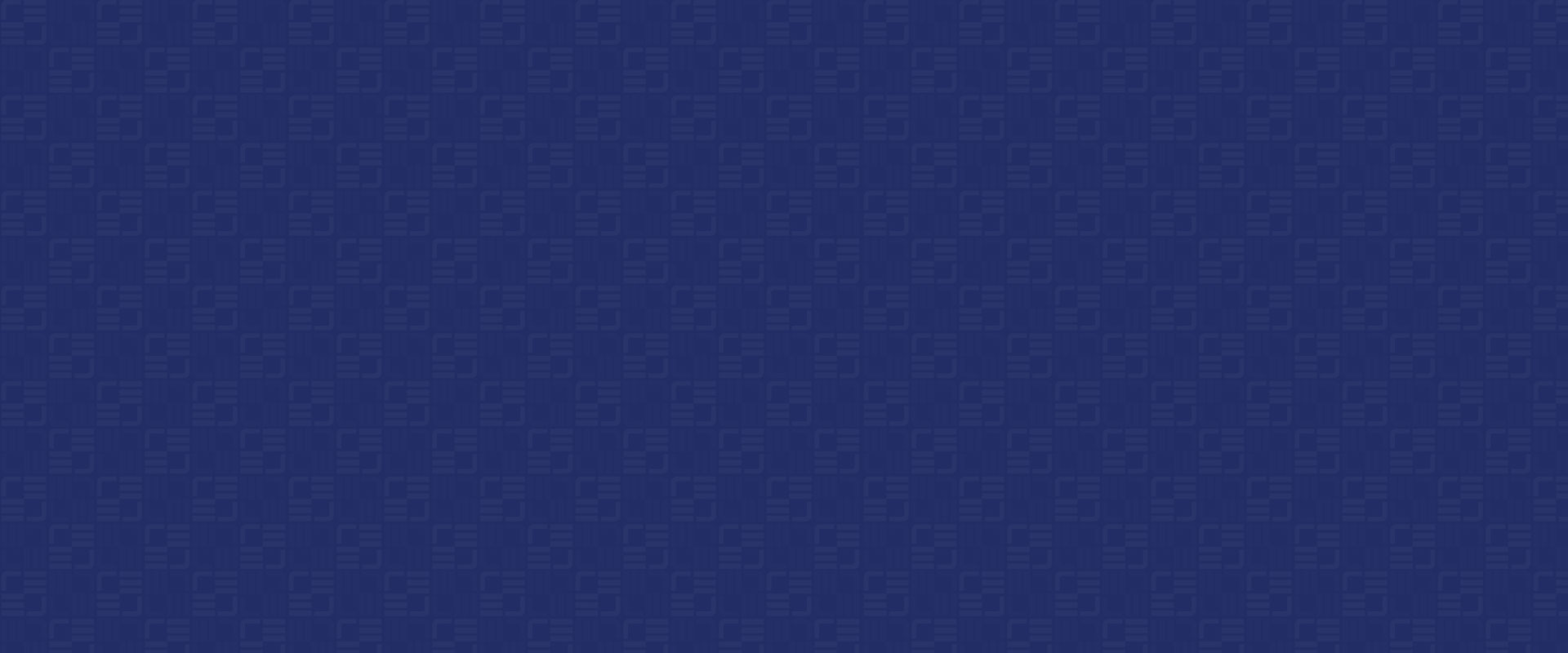
Categories: Cooling Tower.
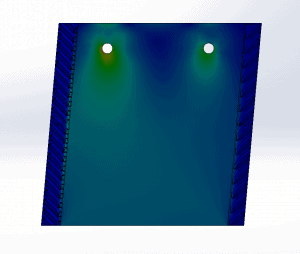
Figure 1: Stress on hanging sheets
As we continue to develop new products, like the XF75Pro, and assist customers all over the world with application questions, it becomes important not just to help with understanding how our products work but also shed some light on why products fail. As discussed above, we consistently receive inquiries regarding the replacement of failing crossflow hanging sheet film fill. Part of educating our customers is helping them understand why their hanging sheets failed to begin with and how upgrading to rigid, structural block fill can prevent future failure.
When we look at a PVC sheet on two rods through openings in the product and apply gravity and a water film weight to it, we can start to see where we have higher stresses in the material. The higher stresses are most likely going to be where we see the initial failure. Hanging sheets experience a distributed stress to the sheet (shown in green on the drawing to the left), stretching it and pulling it downward from its supports. Localized higher forces are seen around the two support openings (depicted in yellow and red). These forces cause a situation where we would expect failure of the sheet starting from the support hole, continuing to the top edge of the sheet and transferring its weight to the sheets next to it. This creates a cascading failure effect in both directions from the initial sheet.
By modeling structural packs with engineered support structures, we set out to see if we could prevent, or reduce, stresses that can cause premature failure. The drawing shows that we have drastically reduced the stress imparted on the product by supporting it over more surface area, thus reducing localized stresses to a fraction of what we see in the hanging sheet model. This would lead us to expect that the plastic product will last longer and also be better prepared to handle any increased weight gain from fouling or scaling.
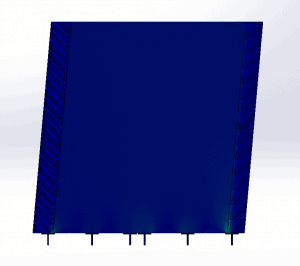
Figure 2: Stress on bottom-supported packs
Following the modeling stage, Brentwood also conducts product testing to verify our findings. This allows us to educate our customers and prevent failure from reoccurring when there is an opportunity to upgrade.
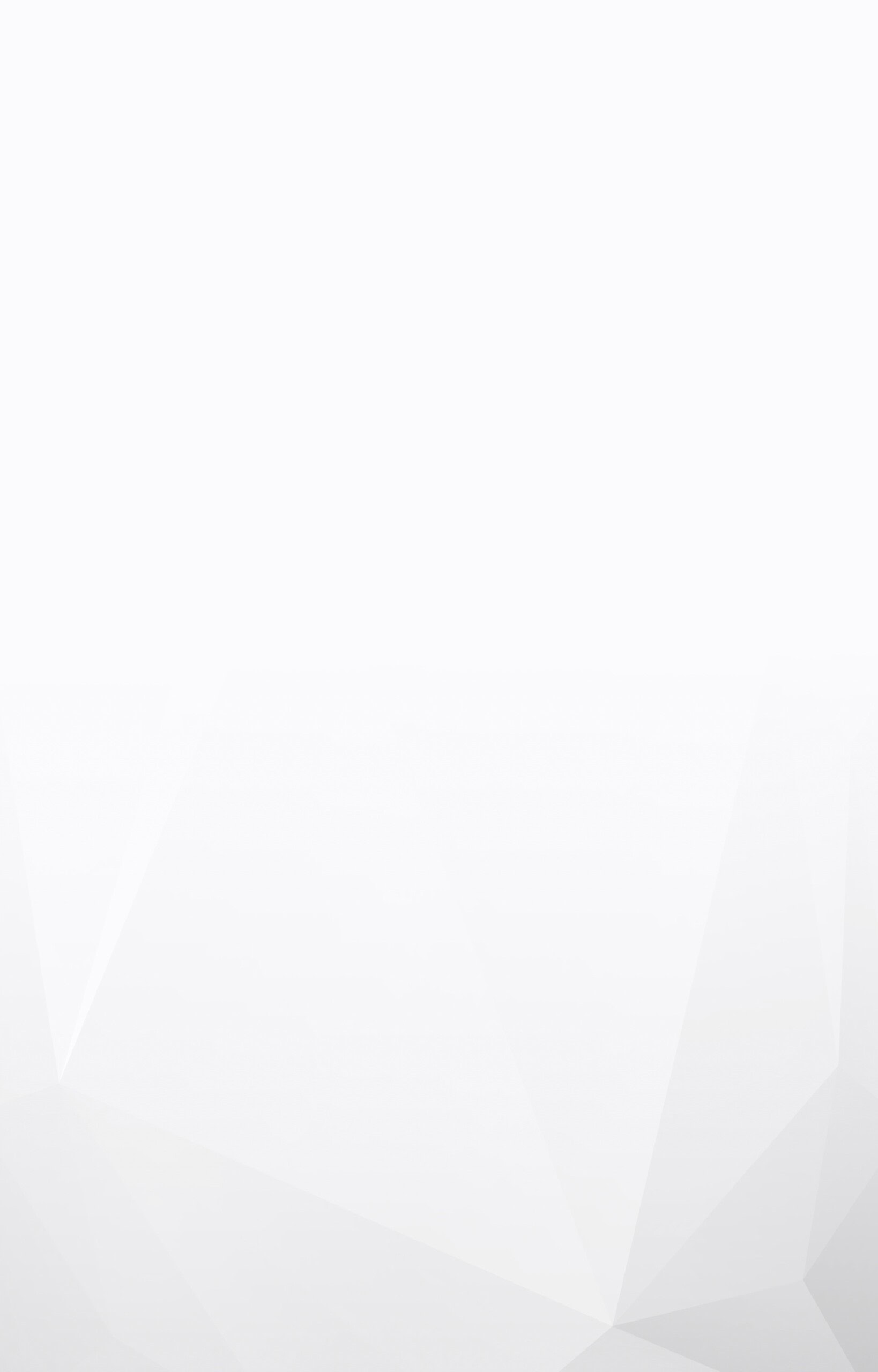