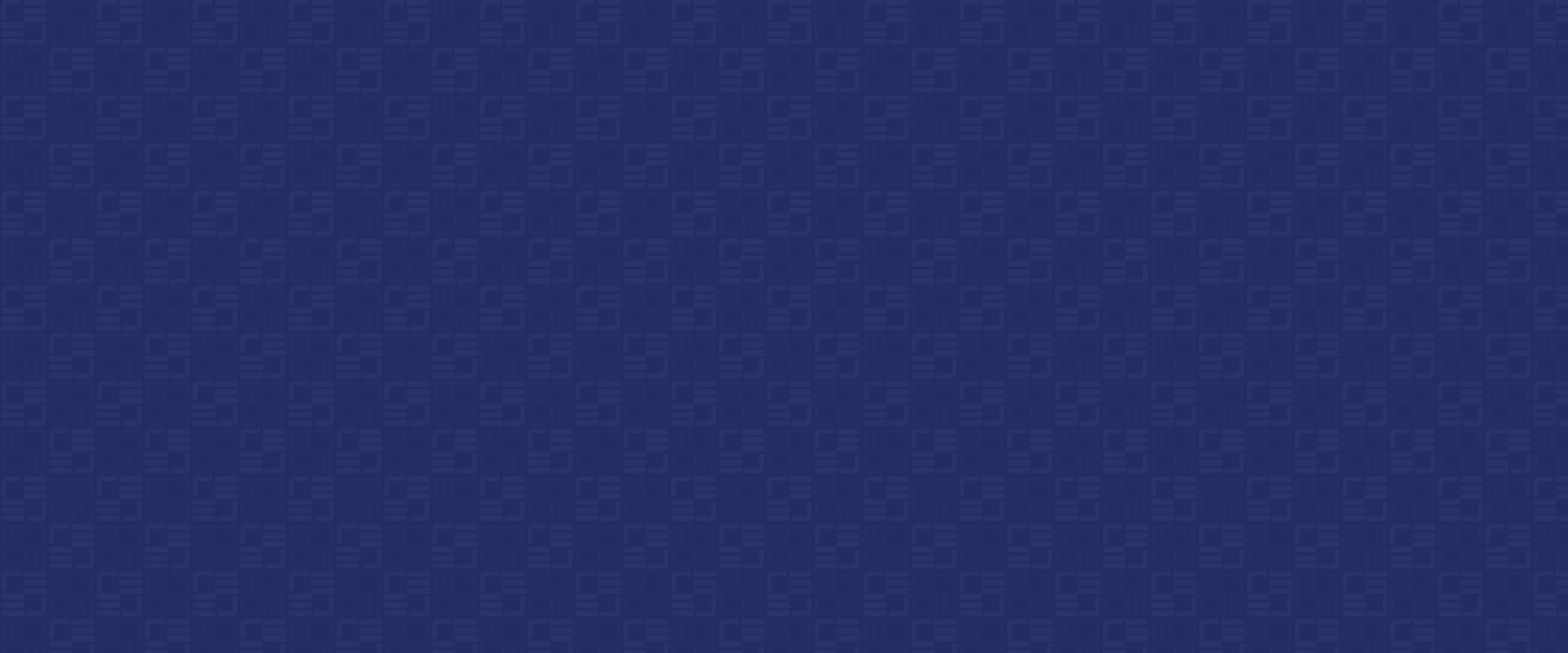
Categories: Cooling Tower.
Splash fills have been used in cooling towers for almost as long as cooling towers have existed. The original splash fill designs of simple wood slats hung in a gridwork system, or platforms made of wood slats, eventually shifted toward plastic shapes and components as the benefits of polymers and their manufacturing methods evolved. As with all fill development work, the goal is to find ways to improve the cooling capacity per unit of fill volume. While film fills have certainly taken this concept to new heights, the anti-fouling benefits of splash fills prove the worth of improving the performance of splash fills.
From product engineering and design aspects, the questions we ask when evaluating a product are: 1) What is actually happening when we test the product? 2) Why is what we’re seeing providing the test results that we’re getting? and 3) What can we do to improve the product, either by preventing something negative that we’re seeing or by causing something beneficial that we’re not seeing? When looking at competitive splash products, especially splash bars, we applied this methodology to various new tests and methods in order to gain a greater understanding of splash fills.
One item that became very evident in our testing of traditional splash bars, – such as V Bar, Kelly Bar, and wood or PVC Lath – and compared to open-mesh type products produced by pulse-extrusion manufacturing, was that the open-mesh products provided a different droplet distribution than the older, traditional splash bars. While providing surfaces upon which the circulating water will impact, creating droplets that provide the name for “splash fills,” traditional splash bars do not provide a uniform distribution of those droplets. Traditional splash bar designs yield concentrations and agglomerations of water where collected water drains off individual splash bars and the droplets combine into larger droplets and even streams of water.
Brentwood used this knowledge when developing SpiraBar to create a splash fill that would provide the most uniform droplet distribution of any splash bar design. This design not only raises the bar on thermal performance but allows the bars to be installed without the staggered configuration that older designs required due to water shedding (comparative illustration below).
Without the need for a staggered configuration, Brentwood realized the opportunity to revolutionize the grid system, as well. The SpeedGrid offers over 800% greater area for bar installation, with a patent-pending design that cuts install time in half. Its QuickLock technology eliminates the need for splash bar fasteners, and the system’s stainless construction provides better corrosion resistance than coated grids.
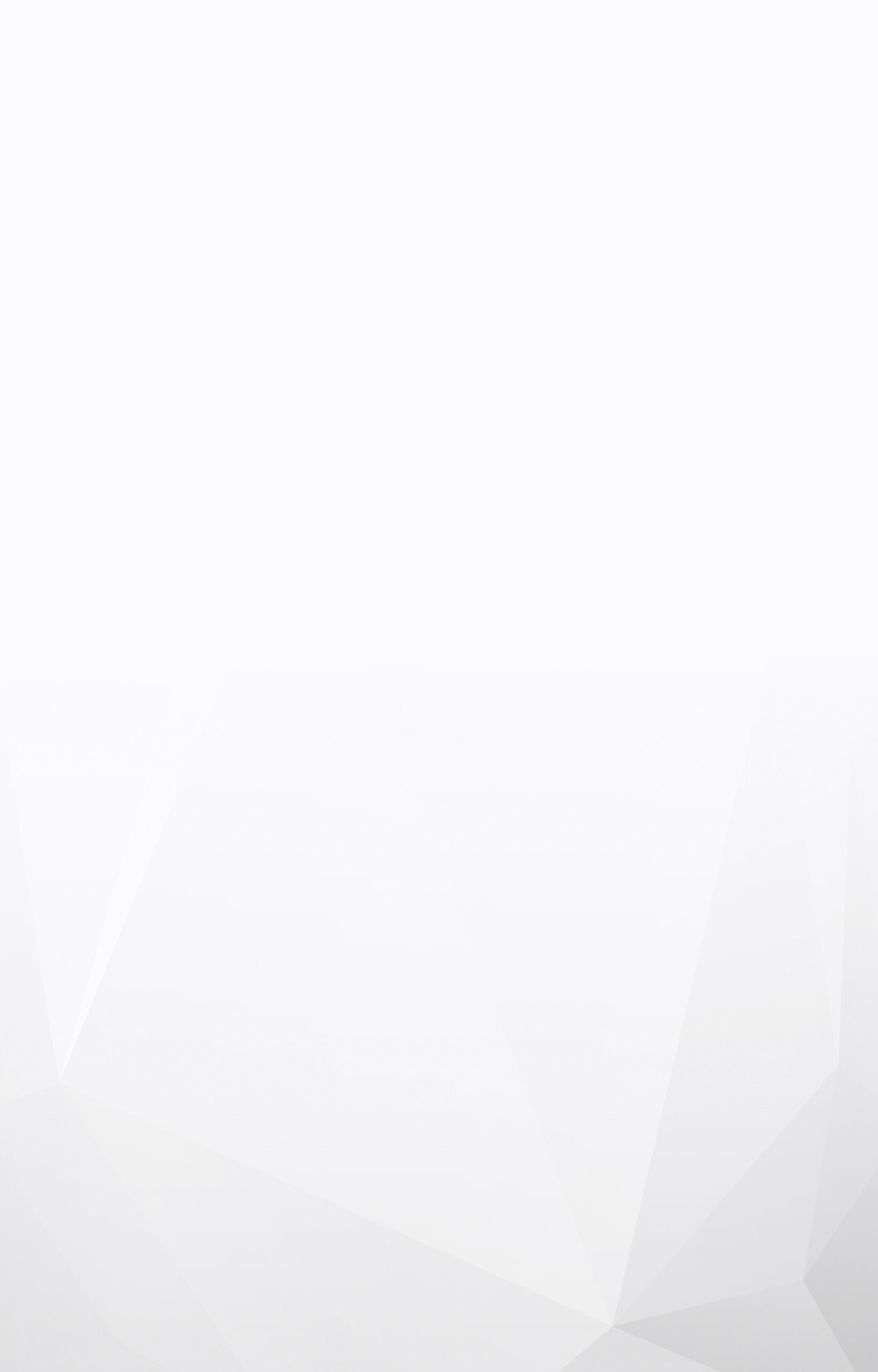