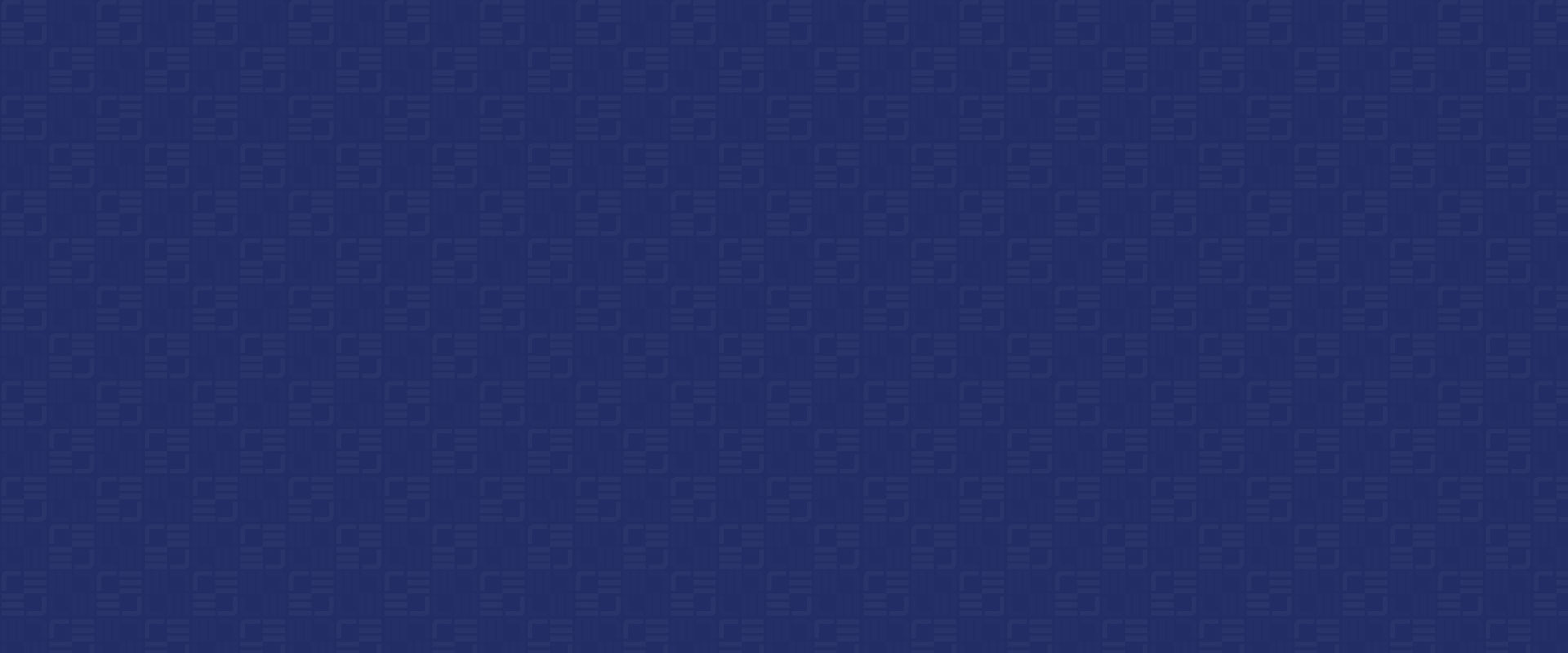
Categories: Cooling Tower.
The petroleum refinery process is both interesting and complex, combining numerous chemical processes to produce an array of products. Cooling systems play an integral part in the production of these products.
Unlike other applications, such as electrical generation or HVAC comfort cooling, petrochem applications pose a unique challenge for water cooling systems: there is a much higher likelihood of oil and grease contaminants being introduced into the cooling system. Whether it’s through leaks in heat exchangers or other equipment, the introduction of hydrocarbons into the cooling water is cause for concern. This is because oils and greases act as a food source for biological organisms.
From past articles on fouling, we know that biological growth is the foundation for fill fouling and cooling tower performance loss. If the biologicals have a steady source of food, they can thrive and grow in the tower, causing issues with both air and water flow as suspended solids adhere to them. Water treatment companies are typically aware of this probability, and therefore, test and treat the water appropriately. However, leaks are a bit trickier; some are easily detected and maintained, but it often takes weeks, or maybe even months, before they are truly corrected. In these cases, having a fill that balances high thermal efficiency and fouling resistance can be a real benefit.
Brentwood’s new Shockwave fill (pictured left) was developed specifically to handle this type of application. Its enhanced vertical flute geometry, PowerCurve design, and unique microstructure allow ShockWave to provide increased thermal performance over existing products on the market while also increasing its ability to fight fouling and weight gain. By reducing biofouling over time, the potential for bio-growth impacting the performance of the product is greatly reduced over offset- and cross-fluted designs.
Products that traditionally offered this capability sacrificed thermal performance to obtain it. Due to advancements in fill design, that is no longer the case. In fact, ShockWave will not only match performance in the majority of cooling towers utilizing an offset- or cross-fluted product, but will likely improve the tower’s capabilities.
In conjunction with proper water treatment, Shockwave provides an added level of safety to make sure any hydrocarbon leaks won’t limit production, keeping your petrochem operation up and running!
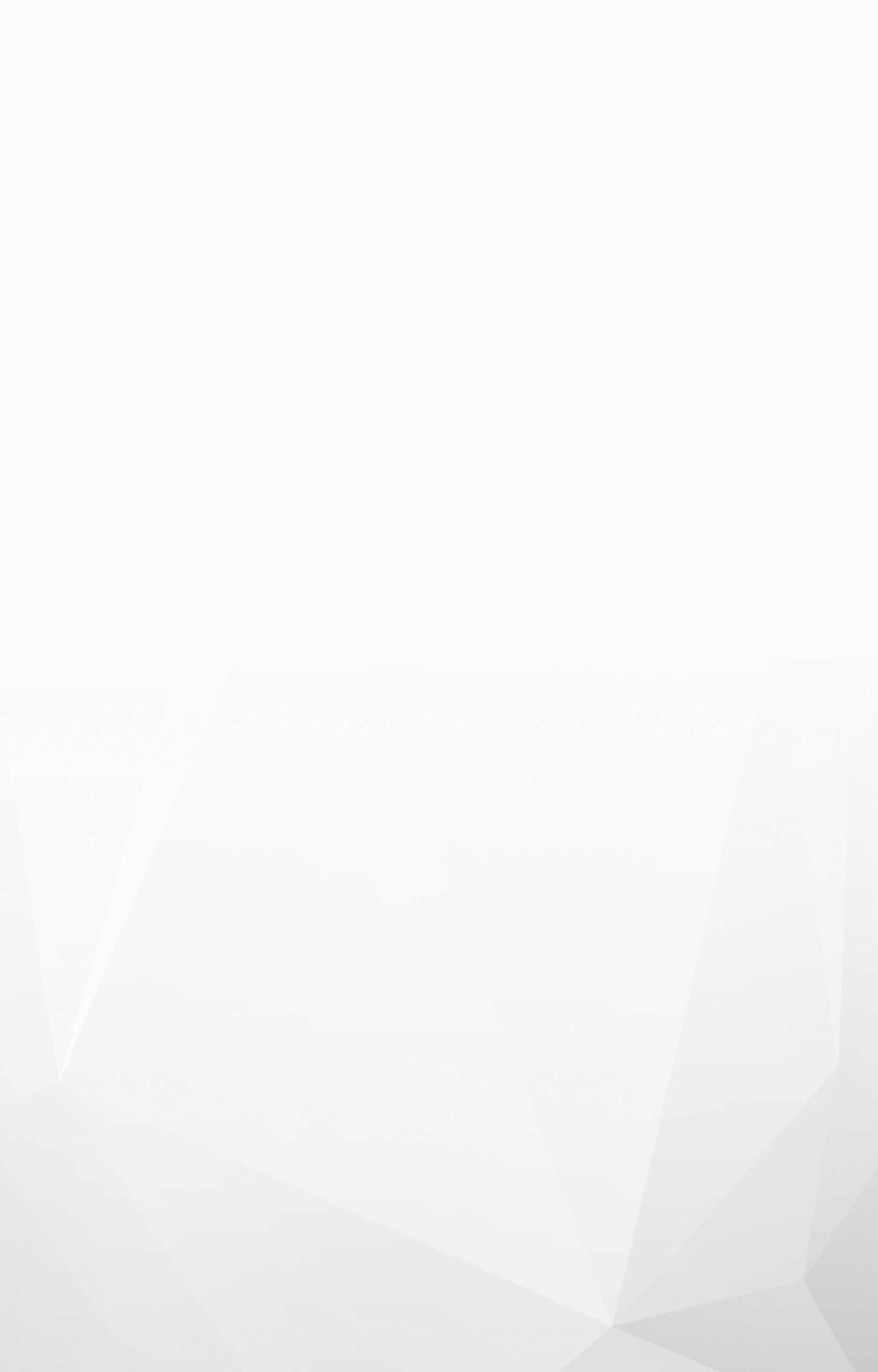