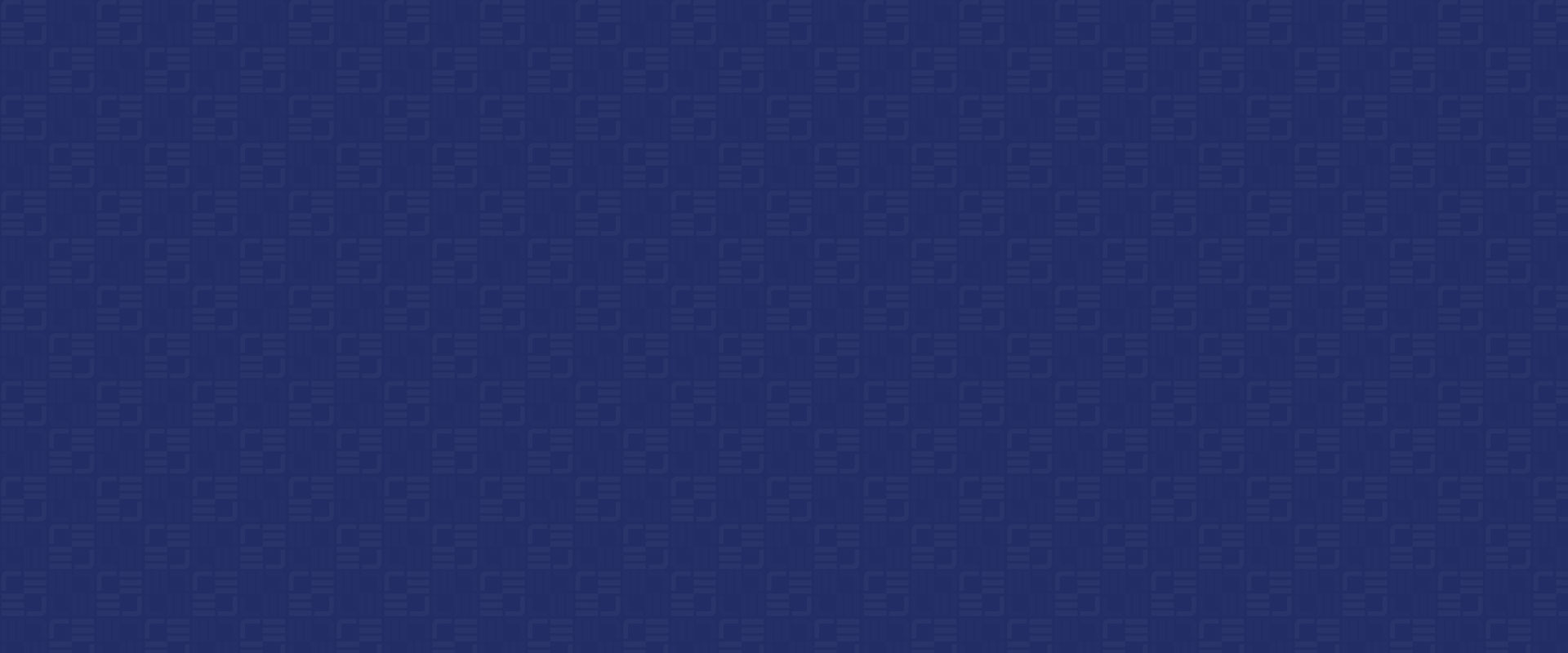
Categories: Cooling Tower.
Brentwood developed its Mechanical Assembly (MA) Technology in the year 2000 as a solution to the industry-plaguing process of gluing plastic sheets together to create fill and drift eliminator packs. The gluing process was time consuming, costly, and released harmful volatile organic compounds (VOCs) into the environment, so our engineering team was in search of a new method that would allow for field assembly.
To mechanically assemble a pack, two sheets are paired together by aligning the male and female attachment tabs. Next, each tab is crimped using a Brentwood “MAssembler.” This is repeated until there are enough pairs to build a pack of the desired width. Finally, the packs are edge-bonded by crimping the attachment tabs on each edge.
Top Three MA Benefits:
Each mechanically assembled pair of sheets is, in effect, a small pack having a very high beam strength proportional to its depth. When pairs are edge-bonded, the resulting pack can support up to 10 times more than the average fill load (the weight of the fill plus the weight of water).
Environmentally Friendly
Over last few decades, American industries have made great strides in reducing air pollution, particularly volatile organic compounds that are found in oil-based plants, auto fuels, and most petroleum products. The Environmental Protection Agency reports that 20 percent of the VOCs discharged into the air are byproducts of industrial manufacturing applications.
At Brentwood, we have been striving to reduce the amount of VOCs in our industrial processes by finding ways to eliminate glue all together. Our mechanical assembly method uses no glue and successfully addresses both the Clean Air Act and OSHA’s Hazard Communication regulation.
Economical & Efficient
There are no glue material or labor costs associated with Brentwood’s mechanically assembled products, so we can pass all savings on to the customer. Even more can be saved on shipping costs because flat sheets are far less expensive to ship than assembled packs.
The process is just as fast gluing and eliminates double handling, meaning packs can be installed immediately after assembly. Brentwood’s MAssembler equipment is simple to set up on-site, easy to use, and available on a per-project basis to further customer savings.
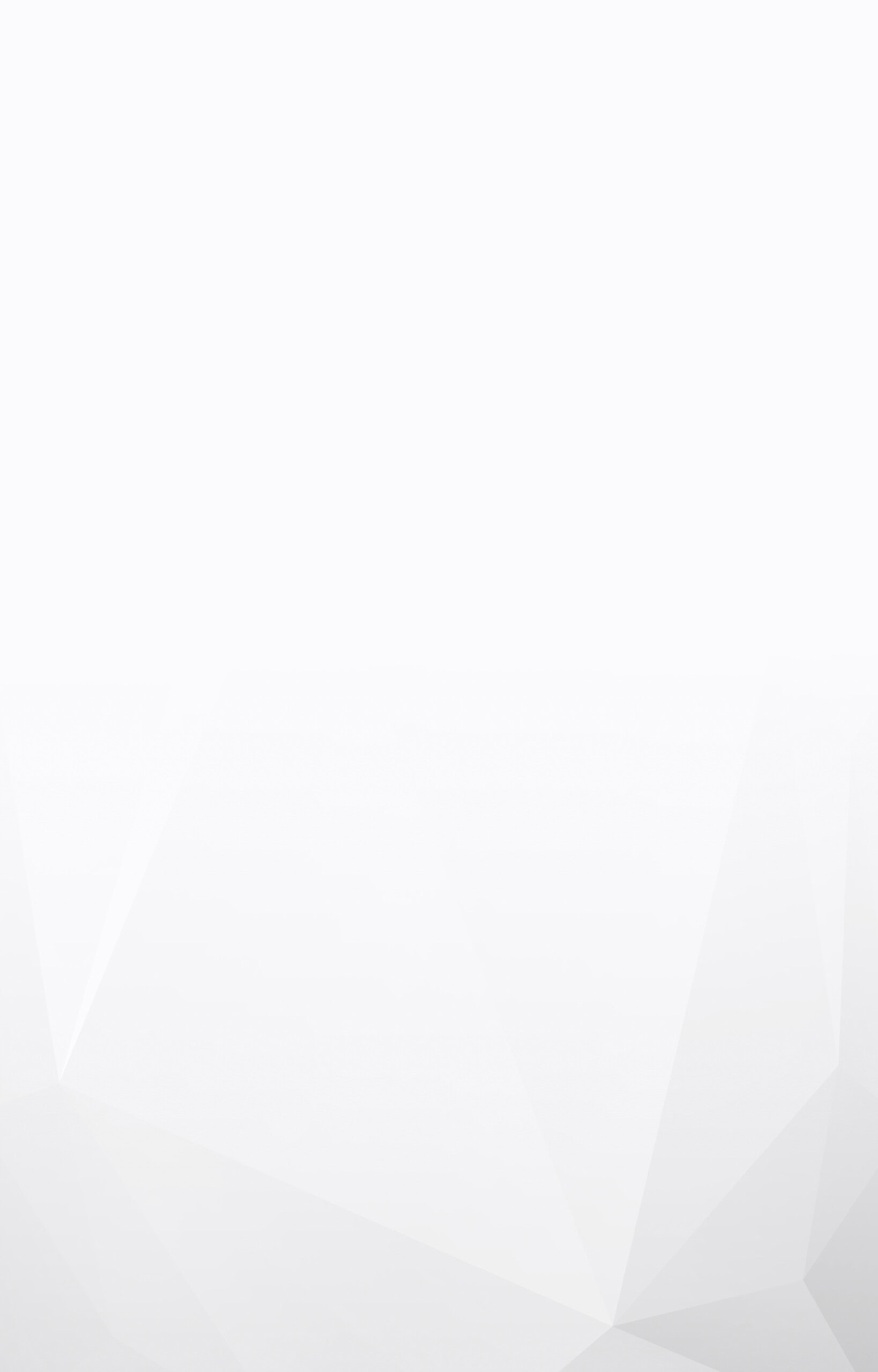