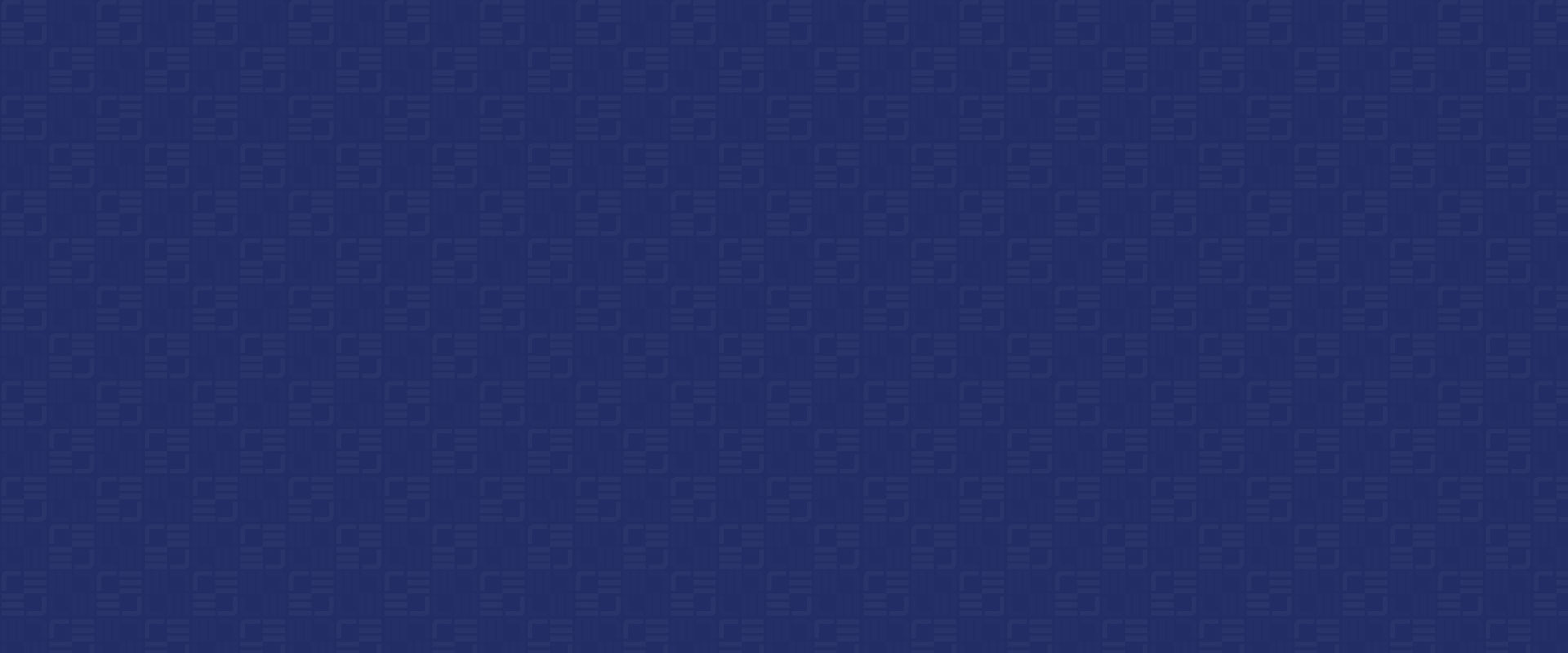
Categories: Cooling Tower.
Why Your Tower May Need Mechanical Filtration
Cooling towers are a type of heat exchanger that use direct contact between air and water to dissipate heat from a process to the outside environment. There are hundreds of processes that cooling towers serve: HVAC systems, power generation, and various manufacturing operations just to name a few. The tower itself is often considered the “simple” part of the cooling process loop, but oversights related to optimization of running conditions and tower maintenance can incur significant costs. A direct contributor to this increase in operating costs is an avoidable condition referred to as fouling.
Fouling is when dirt and other sediment within the system adhere to a microbiological layer, creating an insulating film that wreaks havoc on the thermal conductivity of your heat transfer surfaces. The perfect recipe for fouling within a system is a combination of microbiological growth (bacteria, algae, fungi, etc.) along with suspended solids (dirt, sand, grass, pollen, scale, etc.). Most tower owners incorporate biocides and other tactics within their chemical treatment program to address microbiological growth and the potential health concerns (i.e. Legionella) associated with it. However, an often-overlooked step after chemical treatment is addressing the other half of the fouling equation: suspended solids. The most effective way to handle suspended solids within a system is by incorporating mechanical filtration.
When a tower owner makes the decision that filtration is the next step for their water management program, a quick search on filters can be overwhelming. There will be claims of ultra-fine filtration, high-efficiency filters, filters with low water consumption and annual operating costs – but how can a tower owner sift through all of these offerings to select a filter that is best suited for their application?
There are several considerations to review when selecting a cooling tower filtration type:
Degree of filtration required. A particle size distribution analysis will provide insight on what size (micron) particles are taking up the most volume.
Flow rate. What flow rate does the system need to be able to handle? Is a steady or variable pressure loss preferred?
Installation method. Of the three major installation methods – basin sweeping, side stream, full stream – which will provide the most effective filtration for the application?
Water consumption and maintenance. What is an acceptable amount of maintenance and water loss? Some filtration types require considerably greater backwash (water loss) and routine maintenance than others.
System footprint. Are there space limitations at the desired installation spot? Overall footprint of a filtration system can vary widely depending on the type, flow rate, and installation method selected.
Cost. What is the payback period after evaluating the initial capital investment, annual operating costs, and anticipated savings by implementing a filtration system?
While the above considerations are an excellent starting point, it is not an exhaustive list. Most filtration manufacturers will be more than happy to assist in helping a tower owner select the optimal solution for their specific application. So, let’s review the main cooling tower filtration types, each with their own respective advantages and drawbacks.
Filtration Technology Comparison
Automatic Screen Filters
Automatic screen filters are essentially more advanced basket strainers. A rigid screen with a user-selected orifice opening size allows liquid to flow through while trapping the particles larger than the orifice size. As more particles are filtered from the liquid, the pressure differential across the screen increases and will eventually signal a backwash to begin, cleaning the screen and starting the process over. The unique backwash design of automatic screen filters allows for cleaning without complete reversal of flow.
Pros:
- Capable of removing particles down to 10 microns
- Not affected by the weight of particles to be filtered
- Relatively low water consumption during backwash
Cons:
- Can require frequent maintenance to service components
- Variable pressure differential
Centrifugal Separators
Centrifugal separators create a vortex within a separation chamber that causes solids with a specific gravity greater than water to flow down past a collection plate. Filtered liquid then exits back through the top of the unit, returning to the process. The solids that are separated from the liquid are purged at a user-defined duration and frequency by a motorized ball valve. Separators have been proven to be extremely efficient for particles down to 40 microns. Filtration capability increases as the solids’ specific gravity increases.
Pros:
- Low maintenance requirements (no filters, moving parts, or consumable media)
- Constant pressure differential
- Capable of filtering a large range of particle sizes
- Minimal water consumption during purging process
Cons:
- Limited to solids heavier than water
- Not suitable for ultra-fine filtration
Sand Filters
Sand filters are comprised of a cylindrically shaped vessel that is packed internally with a sand media. Liquid to be filtered is pumped into the sand filter at a low flow rate. As the liquid flows through the vessel, particles are captured within the sand media. The filtered liquid then exits through the bottom of the vessel back to the process.
Pros:
- Capable of removing particles down to 10 microns
- Not affected by the weight of particles to be filtered
Cons:
- High backwash volumes are required to remove filtered particles
- Can require significant maintenance relative to other filtering techniques
- Large space requirements
- Variable pressure differential
- High cost relative to other filtering techniques at the same flow rate
Disc Filters
Disc filters use stacks of discs, typically made of plastic, to filter out particles of a specified micron range. Each disc has etched grooves, that when stacked together under pressure, create intersecting voids to trap particles. As more particles are filtered from the liquid, the pressure differential across the filter increases and will eventually signal a backwash, cleaning the discs and starting the process over.
Pros:
- Capable of removing particles down to 10 microns
- Not affected by the weight of particles to be filtered
- Relatively low water consumption during backwash
Cons:
- Can require frequent maintenance and disc replacement
- Variable pressure differential
While the above filtration types are some of the most common, there are many different filtering technologies available to end users. With all the options out there, it’s key for cooling tower owners to understand the degree of filtration and overall requirements for their application. An in-depth analysis of the pros/cons, risks, and annual operating costs of each type will help promote an informed decision.
No matter the process requiring the cooling, one measure holds true: clean water is a critical step in ensuring your heat exchange equipment is running safely and effectively.
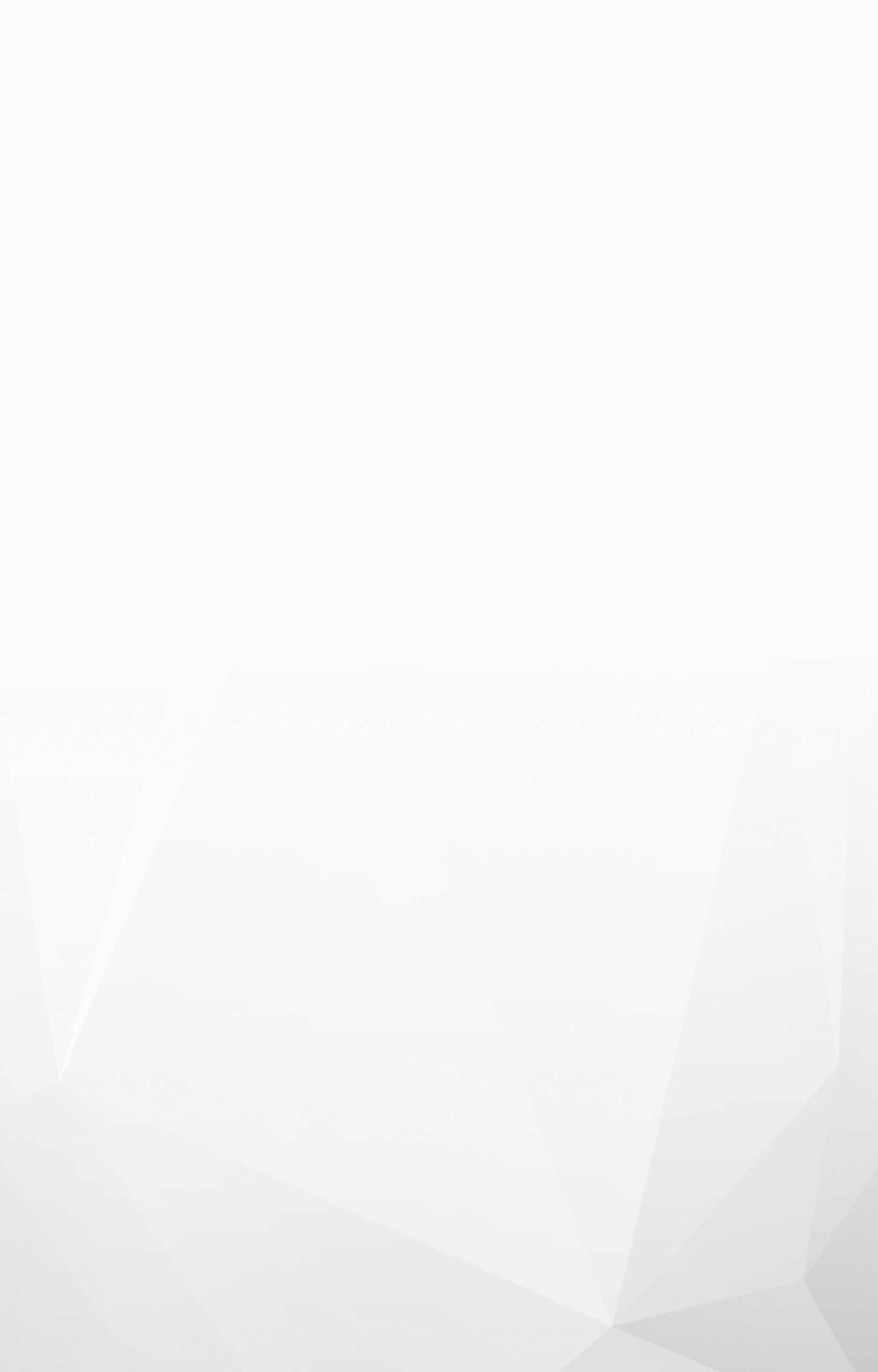