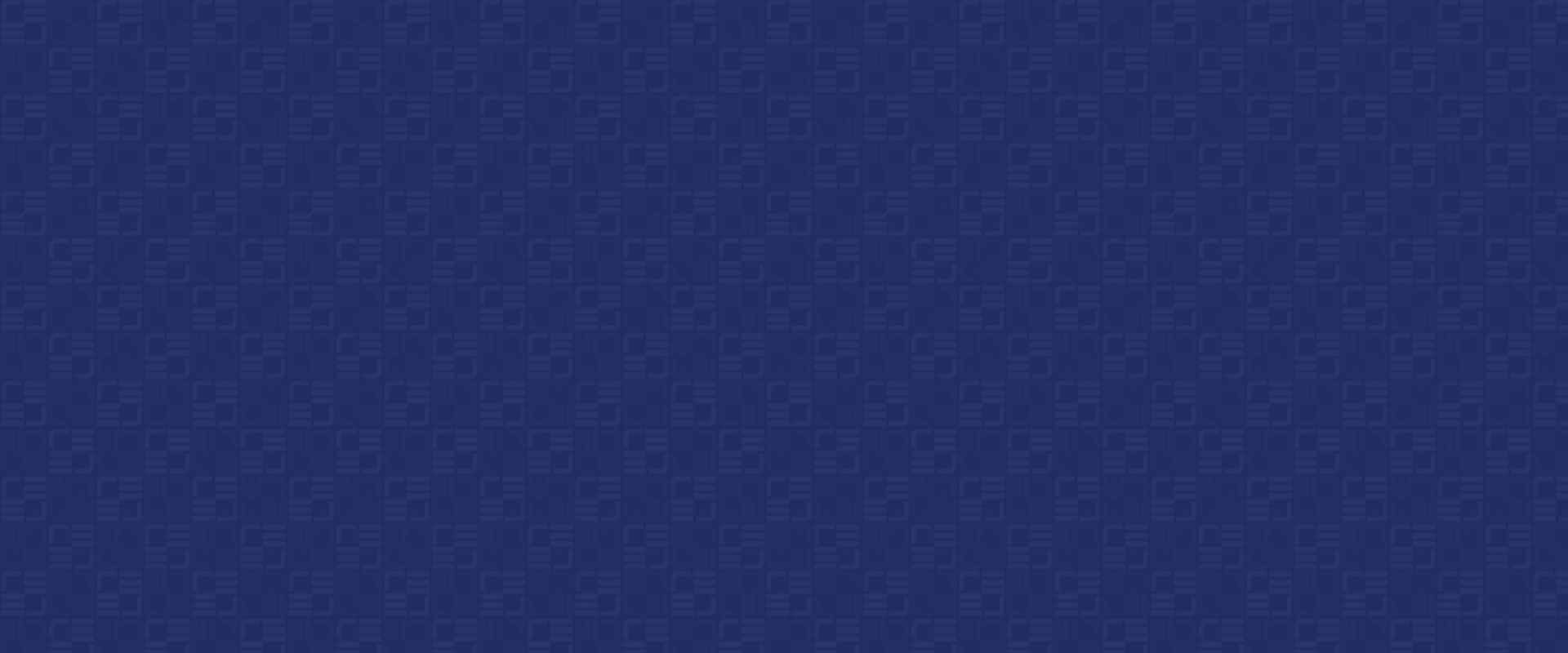
Categories: Cooling Tower.
Some Brentwood products are specifically designed for a single application. One such product is the D15PERF.
The D15PERF was designed intentionally for the turbine inlet market and incorporates a number of features that make it well-suited for this critical application. The pretreatment of the entering air to a turbine is a common occurrence throughout the world. In these applications, whether using cooling coils or humidification via cellulose pads or misters, a droplet eliminator is utilized to make sure any carryover droplets are removed from the air stream. The droplet eliminator is not a very costly component to the entering air system when compared to the filters and other air treatment equipment; however, it is a critical component when it comes to protecting the very expensive machinery downstream. As such, the D15PERF incorporates two very unique features that other “general purpose” products omit from their designs.
Firstly, the D15PERF product does not use any glue in the assembly process. What does this mean for a turbine inlet application? Well, a secondary substance, such as a thermosetting glue, can easily drip during the assembly of the product and leave glue “runners” throughout the sheets of the eliminator. During operation, as air passes over the product and droplets impact the sheets, there is a potential for these “runners” to peel off of the sheets and break free. This debris can then travel downstream into expensive operating equipment and cause damage.
The second important feature is that the D15PERF does not have any saw cuts to the faces of the product. Manufacturers will sometimes assemble a double-wide part in order to save on manufacturing labor and then use a band saw to cut the part in half, producing two finished parts. The cutting produces small plastic chips (“burrs”) which partially melt back to the face of the product after cutting, due to the heat generated by the friction from sawing. When installed in a turbine inlet application, these burrs will eventually work loose from the product and become entrained in the entering air stream of the turbine.
So, while there are competing products similar to the D15PERF, other manufacturers utilize glue for assembly and band saw cutting for cost savings. That said, the products may look the same to the untrained eye, but it is important to be aware that using a “general purpose” eliminator can be very risky in a turbine inlet application. When designing a new system or replacing an existing one, remember the two keys for droplet eliminator success: no glue and no saw cuts!
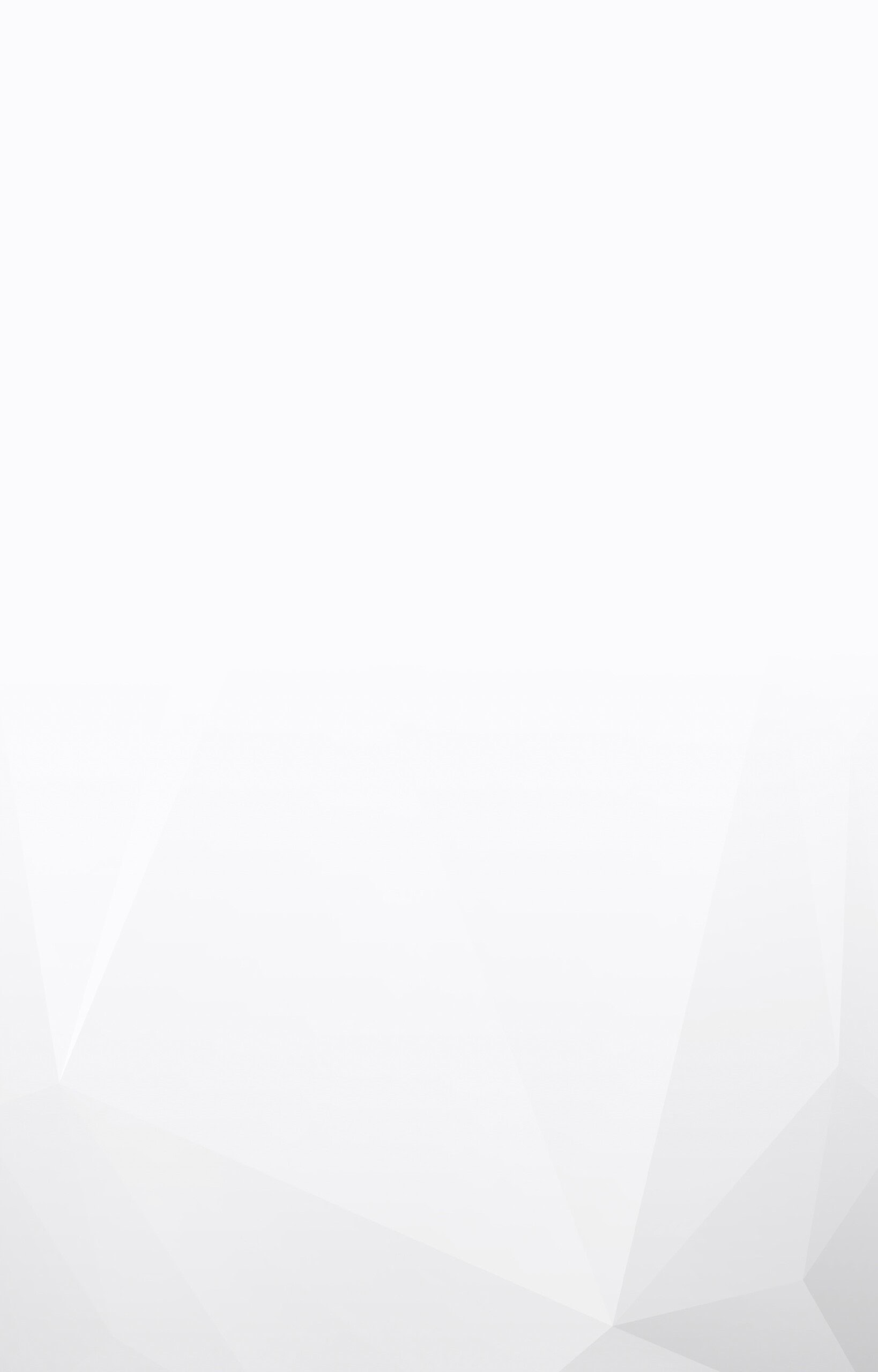