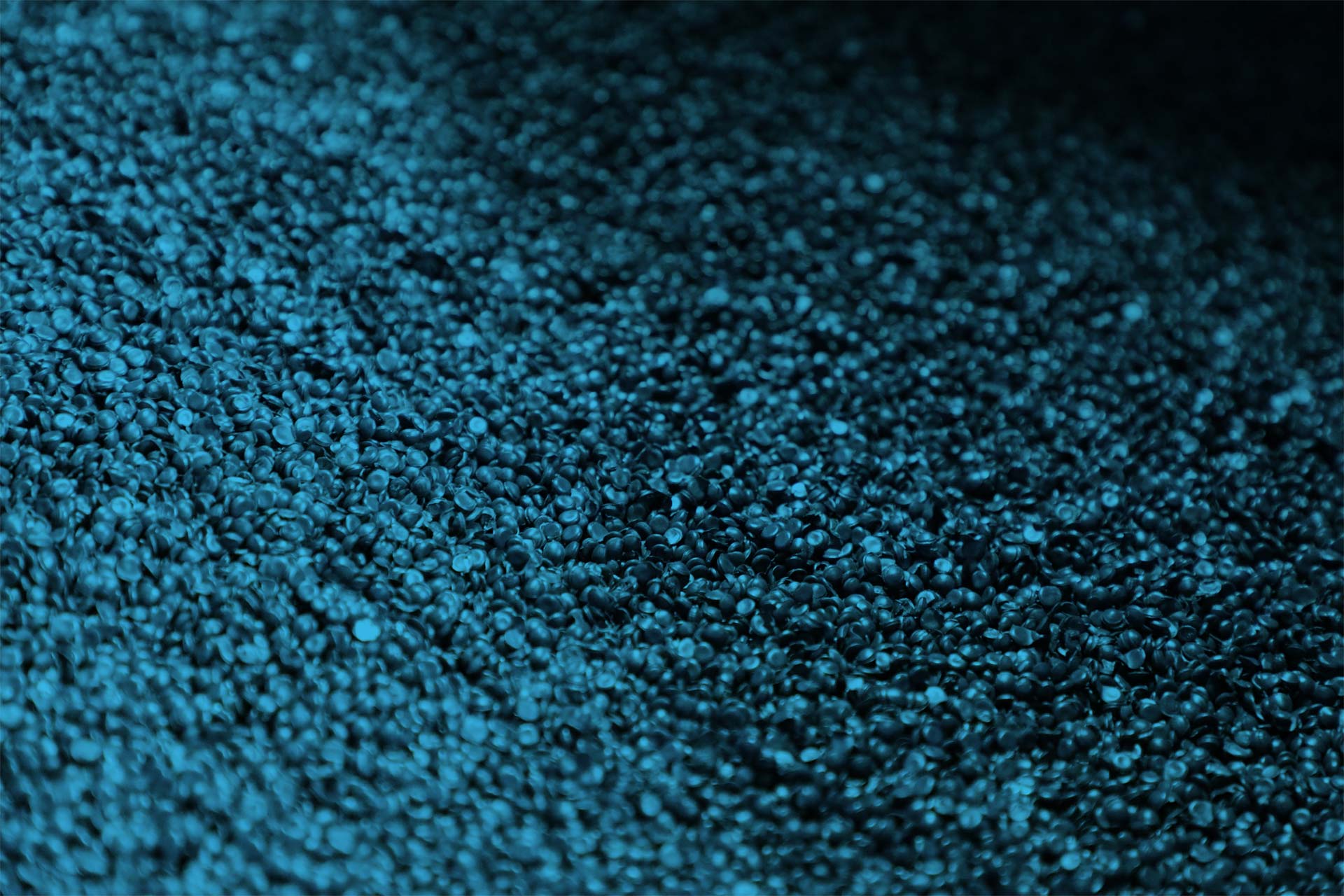
Materials & Resins
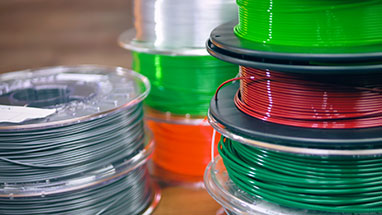
PETG
Polyethylene terephthalate works well for applications that require precision without sacrificing structural integrity. This is especially true for applications that require deep draws, complex die cuts, and precise details.
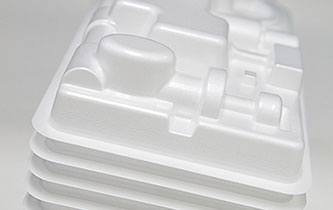
PETG FOAM
This material provides a clean and durable alternative to HIPS for opaque product applications.
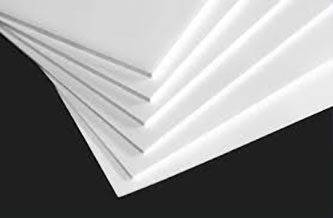
HIPS
High-Impact Polystyrene is a versatile and cost-effective material that is easy to form. Despite its name, HIPS actually provides low impact resistance when compared with other thermoformable materials, as it simply has a higher-impact rating than other materials in the polystyrene family.
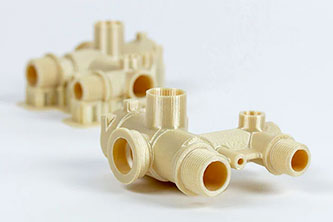
ULTEM
This material offers outstanding thermal resistance, high strength and stiffness, and broad chemical resistance.
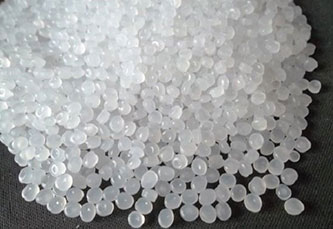
PP
Polypropylene is a cost-effective material that features high flexural and impact strength and is very resistant to absorbing moisture.
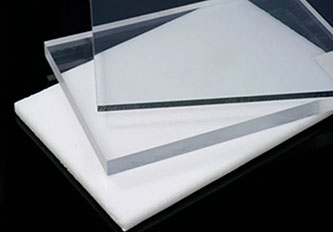
PC
Polycarbonate is extremely durable over a wide temperature range and provides exceptional impact resistance. It also offers high clarity, making it an ideal choice for transparent parts.
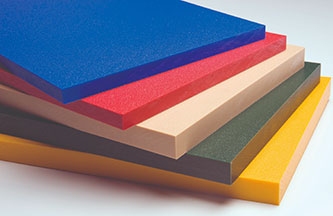
HDPE
High-density Polyethylene is stronger and stiffer than standard polyethylene with good impact and abrasion resistance.
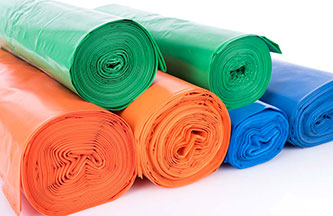
LDPE
Low-density Polyethylene is largely resistant to impact, moisture, and chemicals.
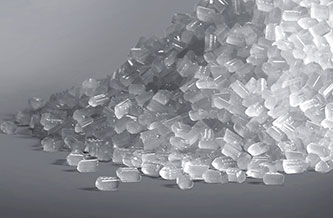
PVDF
Polyvinylidene fluoride is tough material capable of withstanding exposure to harsh thermal, chemical, and ultraviolet conditions.
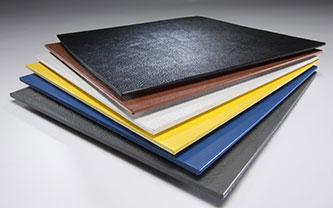
ABS
This material is manufactured by combining three different compounds: acrylonitrile, butadiene, and styrene. In addition to its high stiffness factor and creep resistance, ABS is one of the most versatile plastics available.
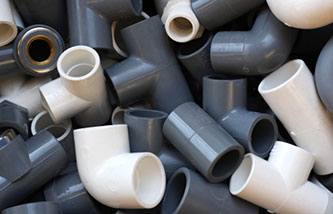
PVC
Polyvinyl chloride is stiffer than ABS and features high-impact strength and natural flame-retardant qualities.

TPO
Thermoplastic Polyolefin is a compounded alloy containing rubber, a blend of polypropylene, and a reinforcing filler. It is a great replacement for metal parts as it provides high impact and chemical resistance.
Films
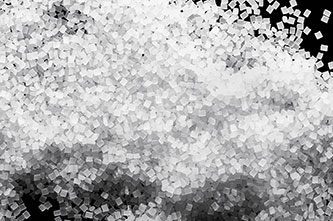
PVDF
Depending on your material selection and project requirements, it may be necessary to cap the chosen material with a film. Films can be protective – to ensure that the material will be durable and long-lasting – or decorative – to enhance aesthetics.
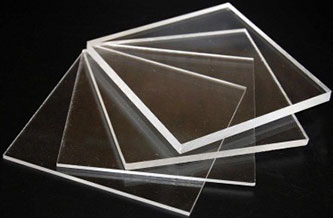
Acrylic
This film is designed to protect materials lacking high impact strength and durability while also providing a shiny, decorative finish.
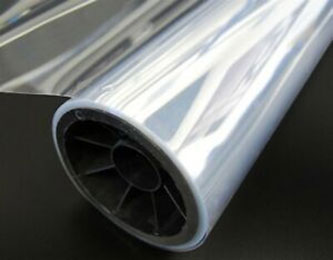
Tedlar®
The Tedlar film is a specialty material designed to combat graffiti, ensuring a clean appearance for the lifetime of the part.
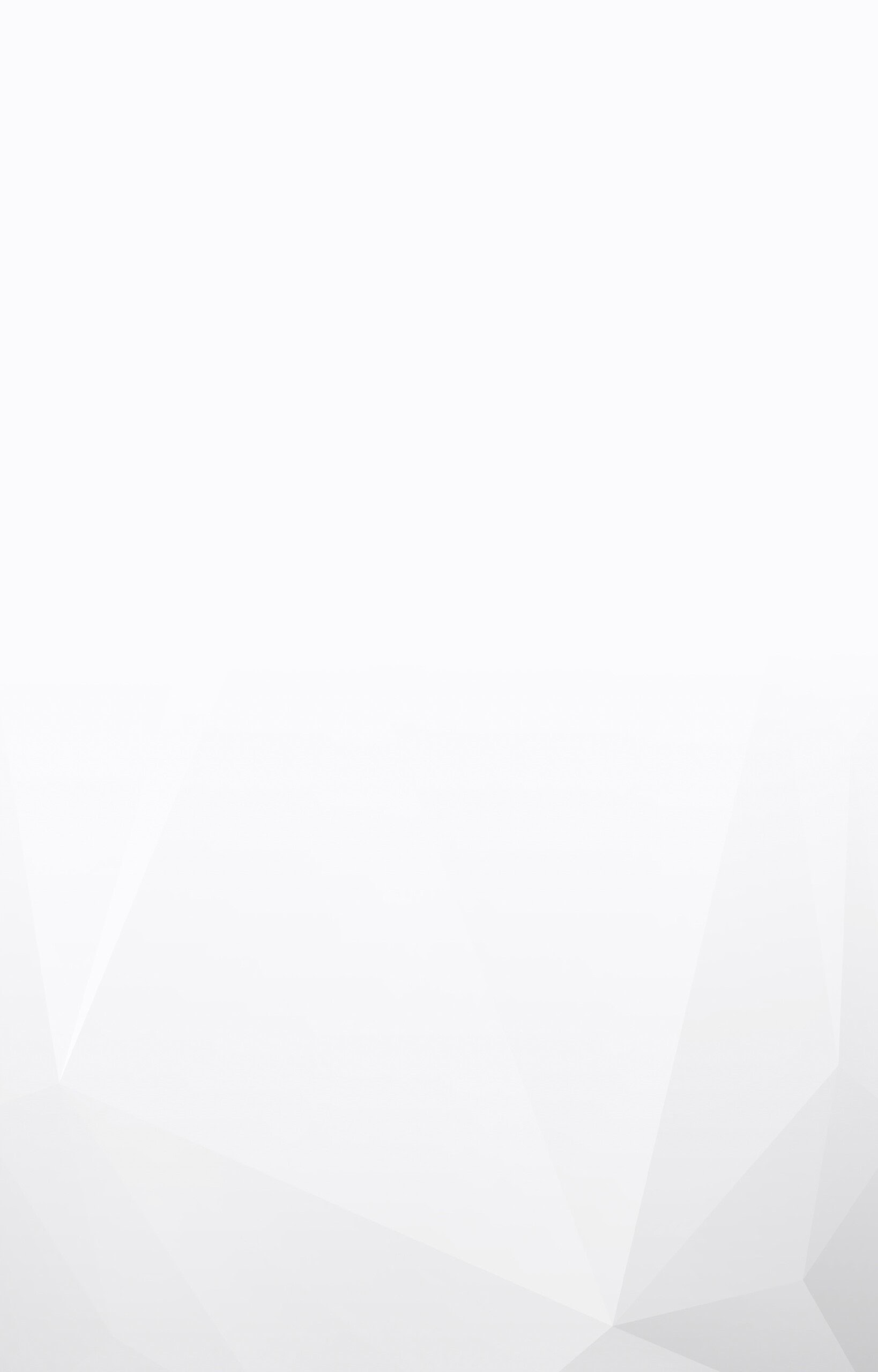