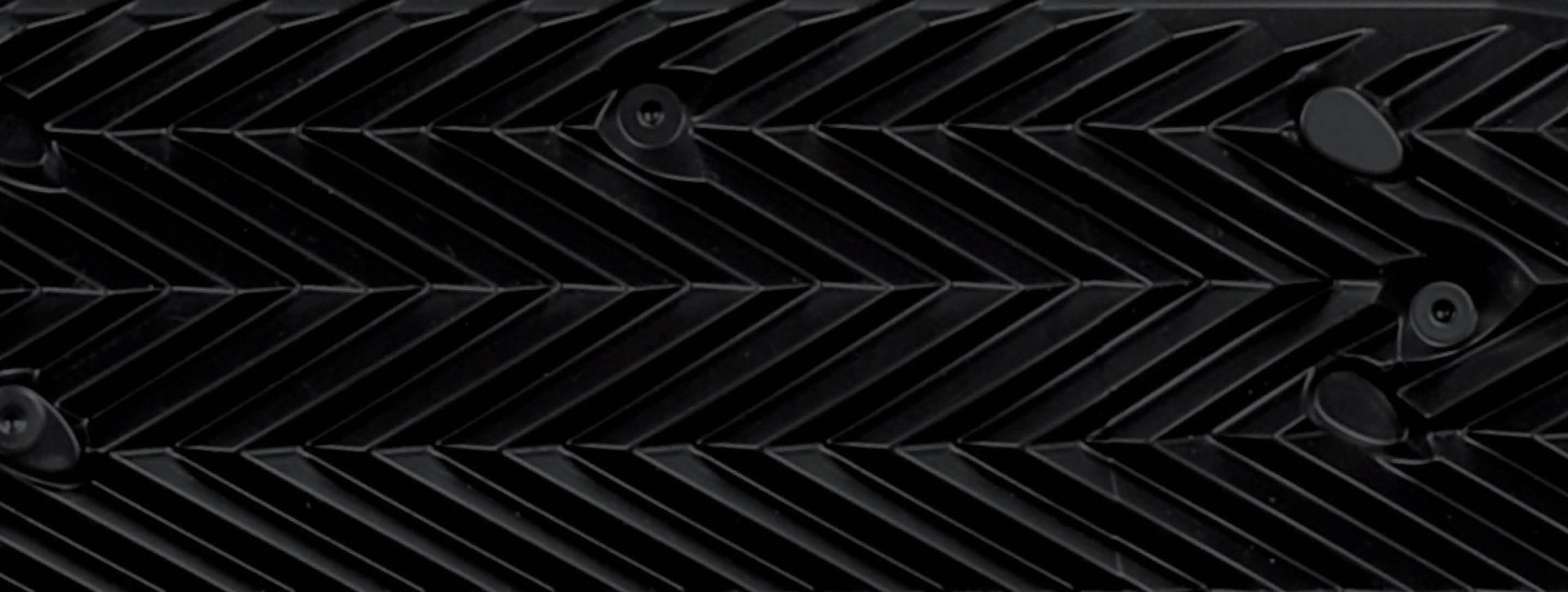
Unmatched Innovation
Click the play button on the video below to learn more about ShockWave, an innovative product offering our team developed as an improvement over traditional vertical-fluted fills.
We're Unmatched.
Testing
Our headquarters in Reading, PA, houses our state-of-the-art R&D lab. The lab is fully staffed by engineers and scientists, and it contains a variety of equipment needed to evaluate cooling tower components. We utilize custom equipment that is designed and constructed to conduct thermal testing as well as measure the fouling propensity of fills, water hold-up weight, and deflection under high temperature, among other key considerations.
New Product Development
Our dedicated R&D team is continuously developing new fills with increased performance and fouling resistance. Our engineers can go from a concept to a physical prototype that is ready to test in a matter of days, allowing Brentwood to rapidly test and iteratively design new products. By using powerful Computational Fluid Dynamics (CFD) software to complete an initial evaluation of fill features, we’re able to determine if a fill looks favorable and print a mold in our large-format 3D printer. The prototype is then thermoformed, assembled, and conditioned for testing.
Assembly Methods
Brentwood’s patented Mechanical Assembly (MA) technology allows fill and drift eliminator packs to be permanently assembled without glue by crimping the male and female attachment tabs molded into the individual sheets. The innovative attachment process produces packs that are exceptionally strong, environmentally friendly, cost-effective, and easily assembled on site.
Brentwood takes pride in being the lone manufacturer with the capability to assemble cooling tower media using each of the four main assembly methods: mechanical assembly (MA), gluing, solvent bonding, and thermal welding.

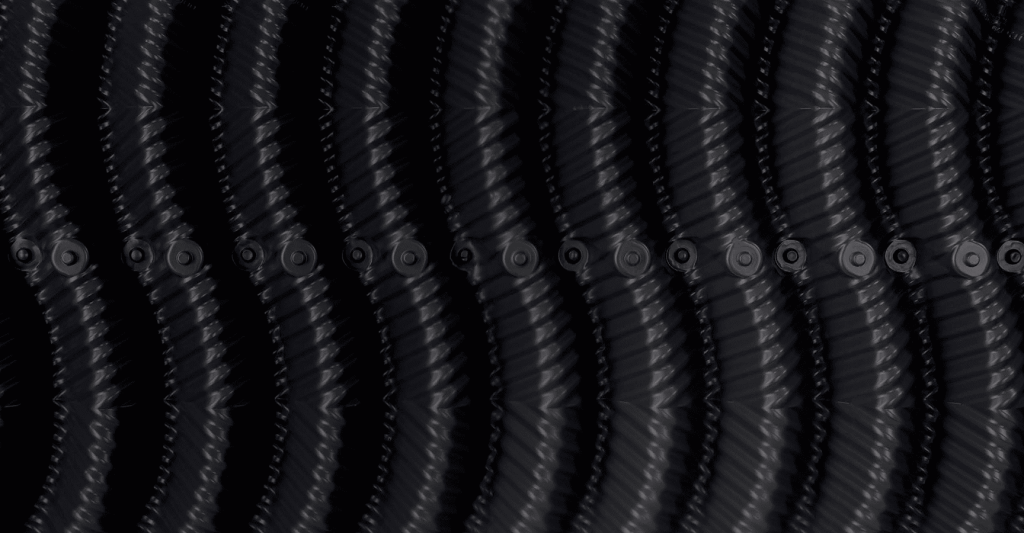
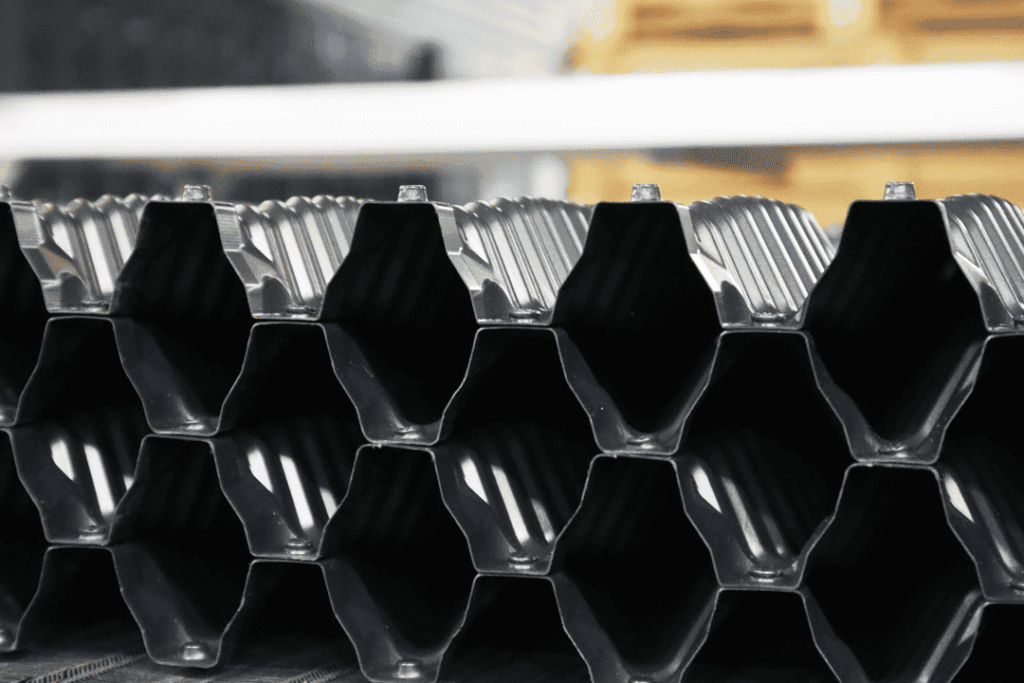
Brentwood is Unmatched.
At Brentwood, we don’t settle for being unmatched; it’s our baseline. Our commitment to surpassing expectations is woven into every interaction as we go the extra mile to serve our customers.
With over 50 years in the cooling tower space, we go above and beyond, consistently delivering results you can depend on. Committed to your future success, we refine and innovate our techniques, designs, and processes, staying ahead of the curve while maintaining stringent quality standards every step of the way.
Choosing Brentwood means choosing confidence. You can trust that our products will not only meet but exceed your expectations and also be backed by our unmatched expertise, innovation, performance, and quality. Your dedicated team is ready to guide you every step of the way today, tomorrow, and together.
Please submit your information to download our brochure.
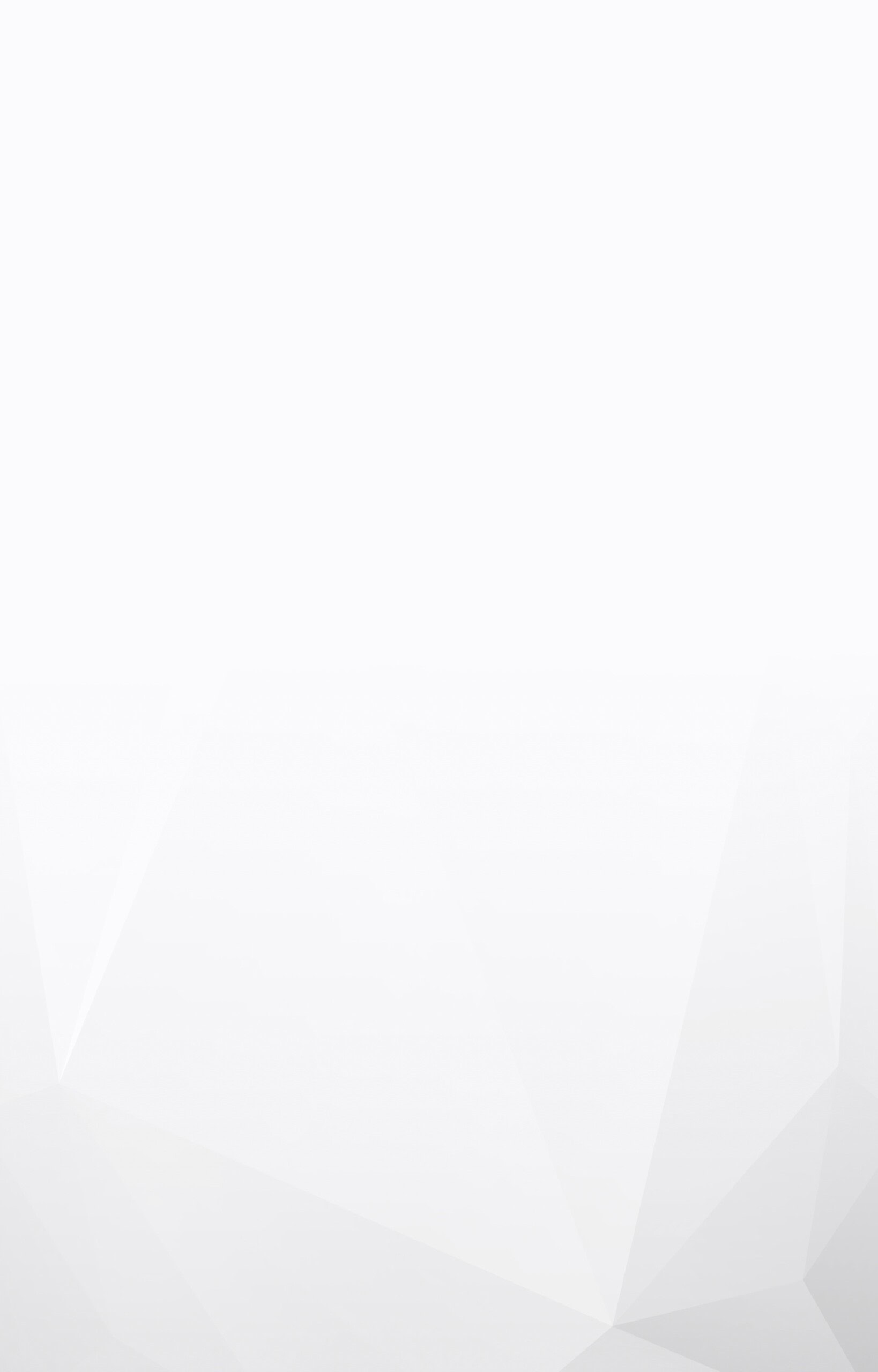